Understanding SolidWorks Simulation Pricing Explained
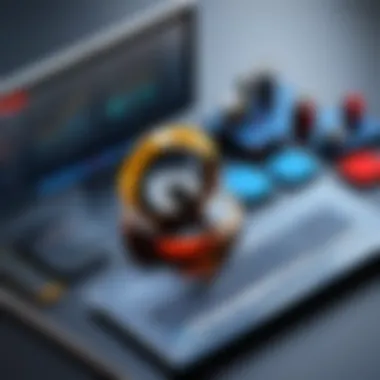
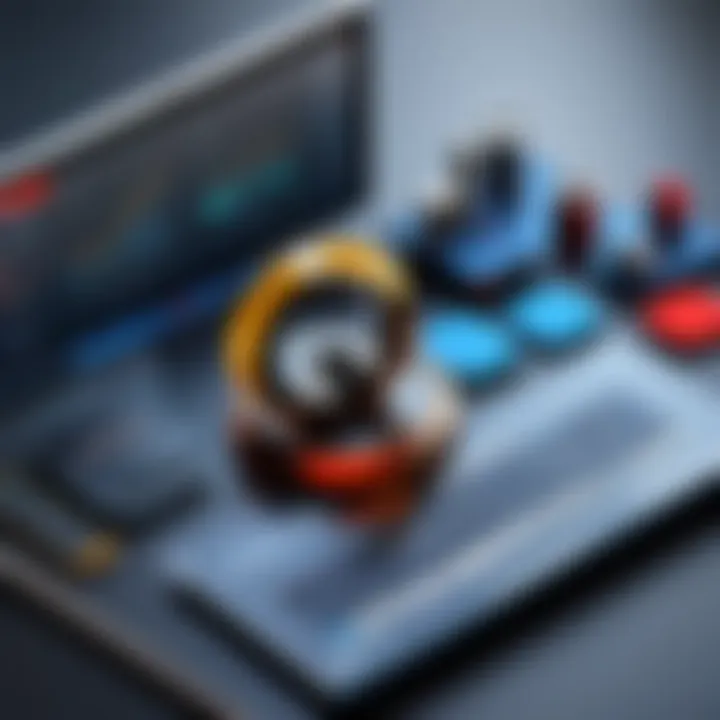
Intro
Diving into the world of SolidWorks simulation is like opening a treasure chest of opportunities, yet, navigating through the pricing maze can be a head-scratcher for many. Understanding the ins and outs of the costs associated with these powerful tools is crucial for engineers and decision-makers alike. This section aims to clarify the landscape of SolidWorks simulation pricing, helping potential users grasp the key elements that dictate their investment decisions.
Imagine a scenario where an engineering firm is on the hunt for a simulation program. They might stumble upon a plethora of options, each with its price tag and unique features. But what really drives these costs? Factors like subscription models, functionality, and value proposition come into play, shaping how a business might allocate its resources.
As we delve deeper, we will uncover the various pricing tiers and distinctive features of SolidWorks simulation, assessing how each aspect contributes to a companyโs bottom line.
Key Features
Overview of Features
SolidWorks simulation offers a range of robust features designed to facilitate complex engineering challenges. It embraces both structural and thermal analysis, catering to diverse project needs. Among the standout features are:
- Real-Time Simulation: Instant feedback allows for quick adjustments, saving time and enhancing efficiency.
- Multi-Physics Analysis: Integrated analysis capabilities enable users to evaluate multiple physical phenomena simultaneously.
- User-Friendly Interface: The intuitive design helps both seasoned professionals and newcomers navigate the software without too much trouble.
These features collectively contribute to the attractiveness of SolidWorks simulation but cost isnโt just about what you get upfront; itโs about the potential returns.
Unique Selling Propositions
What sets SolidWorks simulation apart from the competition? The uniqueness doesnโt merely lie in features; it also encompasses customer support, comprehensive training resources, and an established user community. This support network is crucial for users looking to maximize the return on their investments.
"SolidWorks doesnโt just provide a tool; it nurtures a community that empowers users to optimize their designs."
Pricing Models
Different Pricing Tiers
Understanding SolidWorks simulation pricing models is vital for businesses aiming to choose the right fit for their needs. The pricing typically ranges across various plans, comprising standard, professional, and premium options. Each tier unlocks certain features tailored to different project complexities. In a nutshell:
- Standard: Comes with fundamental simulation tools, best for small projects or startups.
- Professional: Expands capabilities with additional analysis options and enhanced support.
- Premium: Offers a full suite of advanced features, ideal for large-scale operations requiring comprehensive simulations.
ROI and Cost-Benefit Analysis
Investing in SolidWorks simulation can yield substantial returns, provided that the cost-benefit ratio is considered carefully. When evaluating the ROI, factors such as reduced prototyping costs, quicker time-to-market, and the capability to mitigate design flaws early in the development process surface as key points.
Calculating potential savings and efficiency improvements allows firms to justify their expenditureโafter all, investing in the right tools today means fewer headaches tomorrow.
In summary, understanding the pricing of SolidWorks simulation equips engineering firms with the knowledge to make wise choices, ensuring that money spent translates to value gained.
For further reading on SolidWorks simulation and its features, feel free to visit Wikipedia, Britannica, Reddit, or Facebook.
Foreword to SolidWorks Simulation
In today's competitive landscape, the integration of advanced tools like SolidWorks Simulation into the engineering design process is becoming a linchpin for efficiency and innovation. Understanding SolidWorks Simulation is crucial not just for engineers, but also for decision-makers who oversee resource management and strategic planning. As businesses navigate the complexities of modern product development, having a robust simulation tool at their disposal can transform how they approach design and testing.
The Role of Simulation in Engineering Design
Simulation plays a pivotal role in modern engineering design. It allows engineers to create virtual prototypes of products and test various scenarios without the costly investment in physical models. For instance, consider a team working on a new bicycle frame. By employing SolidWorks Simulation, they can analyze different materials under various stress conditions, visualize performance outcomes, and optimize for weight and strength before ever cutting a piece of metal. This not only saves time but also minimizes the financial risks associated with trial-and-error approaches.
Furthermore, simulation enables teams to iterate designs rapidly. Engineers can tweak parameters, test hypotheses, and gather invaluable data with just a few clicks, rather than weeks or months spent on physical build-outs.
"Simulation is the safety net that catches the flaws before they hit the market โ it's a game changer."
Overview of SolidWorks as a Simulation Tool
SolidWorks stands out in the world of CAD software, particularly for its comprehensive simulation capabilities. It offers a user-friendly interface combined with powerful analytical features. Users can easily navigate through various modules tailored for specific needs, such as fluid dynamics, structural analysis, and motion studies.
One notable element of SolidWorks Simulation is its integration with the core SolidWorks CAD application. This means that users can switch seamlessly between designing and testing without the need for extensive external software. The results provide immediate feedback, which is pivotal for making design decisions quickly and effectively.
A distinguishing feature of SolidWorks is the wide array of analysis types it encompasses. From linear static and dynamic analysis to advanced nonlinear and thermal analysis, the tool's versatility caters to diverse industries. Additionally, it can handle complex geometries like those found in automotive or aerospace applications, proving invaluable in high-stakes engineering environments.
Factors Influencing SolidWorks Simulation Pricing
Understanding the nuances of SolidWorks simulation pricing is vital for businesses that seek to optimize their engineering processes. Pricing isn't a one-size-fits-all affair; it shifts and morphs, influenced by several key factors. By delving into these elements, users can gain invaluable insights that help in making economically sound decisions, ultimately leading to better utilization of resources and enhancements in productivity.
Licensing Models Explained
The choice of licensing model plays a huge role in the overall cost associated with SolidWorks simulation. Companies typically have two options: perpetual and subscription licenses. A perpetual license is a one-time purchase that grants indefinite use of the software, but it may require additional annual fees for upgrades. This option tends to be appealing for firms that prefer ownership and plan to use the software long-term.
On the other hand, subscription licenses involve regular payments, usually monthly or annually. This option might seem less daunting at first glance, as it lowers the initial barrier of entry and allows for more flexibility. However, over time, subscription costs can accumulate, so businesses need to crunch the numbers to see which option aligns better with their financial plans.
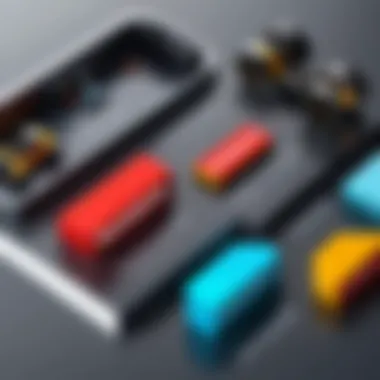
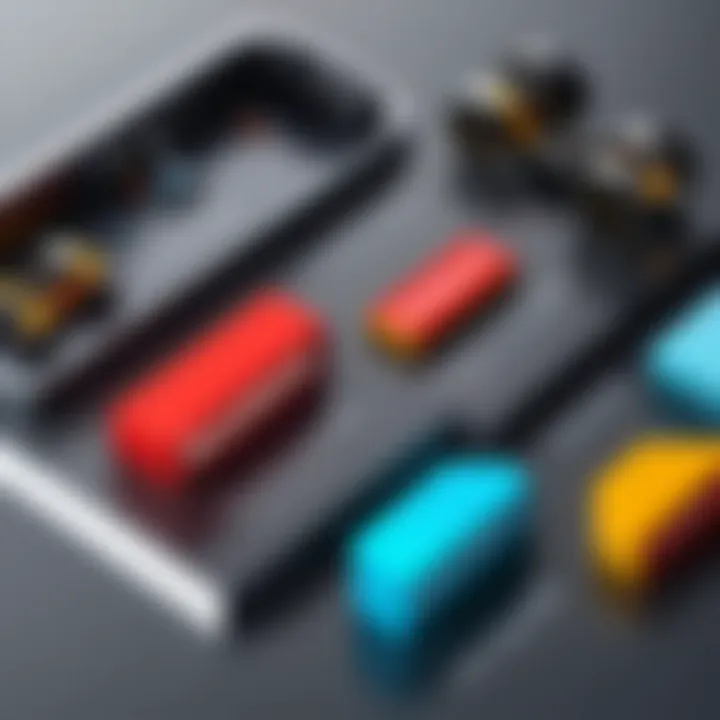
"A license is more than just a purchase; it's an investment in the future of your engineering capabilities."
Feature Sets and Their Impact on Cost
Another pivotal aspect in understanding pricing is the interplay between feature sets and costs. Different SolidWorks simulation components come equipped with unique functionalities, which can dramatically influence pricing. For instance, the Standard package offers basic simulation capabilities suited for entry-level designers, while advanced packagesโlike SolidWorks Premiumโgrant access to sophisticated features such as fluid flow analysis and thermal simulation.
Choosing a higher-tier package often means a steeper price tag, but it can offer substantial long-term benefits such as improved design accuracy and faster product iterations. Companies must carefully assess their needs against what each package offers. At times, opting for additional features can yield significant savings down the line by reducing errors and streamlining the design process.
User Count and Multi-user Discounts
User count is yet another consideration that can sway SolidWorks simulation pricing. Most vendors offer tiered pricing based on the number of users; additionally, multi-user licenses can lead to significant savings. For instance, a company with five engineers may find that negotiating a bulk purchase allows for reduced per-user costs compared to individual licenses.
Furthermore, itโs also worth exploring whether the vendor offers discounts for educational or non-profit organizations. Often, investing in licenses for teams instead of individuals can provide a more cohesive working environment while keeping costs in check. When handling multi-user scenarios, itโs wise to consider both the purchase price and the potential for future growth to ensure sustainability in resource allocation.
SolidWorks Simulation Licensing Options
Understanding the licensing options for SolidWorks Simulation is critical for businesses considering their software acquisition strategies. Licensing directly affects the total cost of ownership and the flexibility in use of powerful simulation tools. SolidWorks offers various licensing pathways, each with distinct advantages and considerations. Companies must thoroughly evaluate their project needs, budget constraints, and future growth potential. In this section, we delve into the specific licensing types available, examining their implications for cost efficiency and operational effectiveness.
Perpetual Licensing versus Subscription Licensing
When businesses decide on a licensing type, they are essentially choosing between two main options: perpetual licensing and subscription licensing. Perpetual licenses allow users to own the software indefinitely after a one-time payment. This model appeals to organizations that prefer a capital expenditure over operational expenditure. On the other hand, subscription licenses require ongoing payments usually billed annually or monthly. This approach grants users continuous access to software updates and technical support, and it may suit companies that need flexibility to scale as project demands fluctuate.
Each model comes with pros and cons.
- Perpetual Licensing
- Subscription Licensing
- Pros:
- Cons:
- One-time purchase leading to long-term cost savings if used for many years.
- Ownership of the software without recurring fees.
- Higher upfront cost, which can strain budgets.
- Responsibility for maintaining software updates and support can fall heavily on IT teams.
- Pros:
- Cons:
- Lower initial cost, easier cash flow management.
- Access to the latest features and updates without additional costs.
- Recurring obligations can accumulate into significant long-term expenses.
- If a project turns inactive, continuing payments might feel like throwing money down the drain.
Ultimately, the decision hinges on the financial strategy and specific operational needs of the business. A careful analysis should guide this choice to ensure that it aligns with broader business goals.
Annual and Monthly Subscription Plans
Subscription plans can further be differentiated into annual and monthly options. The crux of this differentiation comes down to flexibility and financial planning.
- Annual Subscription Plans:
Organizations opting for the annual plan typically benefit from a more stable financial forecast as they commit to a once-a-year payment. With an annual subscription, users often receive a discounted rate compared to monthly payments, making it an attractive option for firms that foresee ongoing projects throughout the year. - Monthly Subscription Plans:
This plan offers the ultimate flexibility, allowing companies to subscribe as needed. It's ideal for businesses facing seasonal projects or looking to start small before expanding their capacity. However, the per-month fee can quickly add up, so the long-term costs may exceed that of annual subscriptions if usage extends over many months.
"Choosing between annual and monthly subscriptions requires evaluating project timelines and budgetary constraints to avoid potential financial pitfalls."
Such considerations are pivotal for smaller companies or startups that may need to regulate cash flow closely while still accessing robust simulation tools.
Educational and Non-Profit Discounts
In recognition of the range of users who may face budget restrictions, SolidWorks extends special licensing options for educational institutions and non-profit organizations. These discounts are designed to make simulation technologies more accessible.
- Educational Discounts:
Students and educators can benefit significantly from lower pricing, facilitating the integration of SolidWorks Simulation into learning environments. This opens doors for future engineers to gain hands-on experience with industry-standard tools without burdensome costs. - Non-Profit Discounts:
Non-profit organizations focused on community service or research may qualify for subsidized pricing. These initiatives acknowledge the contributions of such entities, allowing them to leverage powerful simulation capabilities that would otherwise be financially daunting.
In focusing on these specialized discounts, SolidWorks fosters a more inclusive approach to engineering education and innovation, paving the way for the next generation of design professionals.
Evaluating the Total Cost of Ownership
When planning for SolidWorks Simulation, understanding the total cost of ownership (TCO) becomes essential. This concept goes beyond the sticker price of the software. It's a multi-faceted analysis that takes into account all factors contributing to costs over time. For businesses, especially those looking to maximize return on investment, considering TCO might just save you a pretty penny down the line.
Maintenance and Support Costs
Maintaining SolidWorks Simulation isn't just about ensuring the software runs smoothlyโit's about having access to tech support when you hit a snag.
The maintenance and support costs often include:
- Annual fees for software updates: Staying current ensures you benefit from the latest features and bug fixes.
- Tech support subscriptions: Having a reliable support team to troubleshoot issues can prevent prolonged downtimes, affecting productivity.
- Training and resources: Investing in staff training to fully utilize the software may seem costly upfront, but can yield high dividends in terms of efficiency.
Considering these elements can often lead to a clearer picture of ongoing financial obligations, which can add up faster than one might assume.
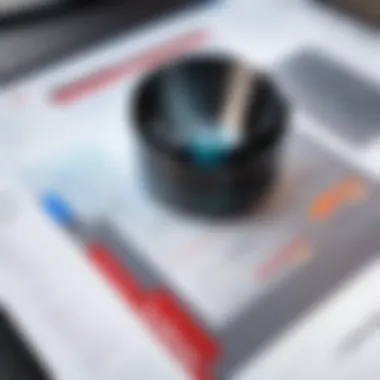
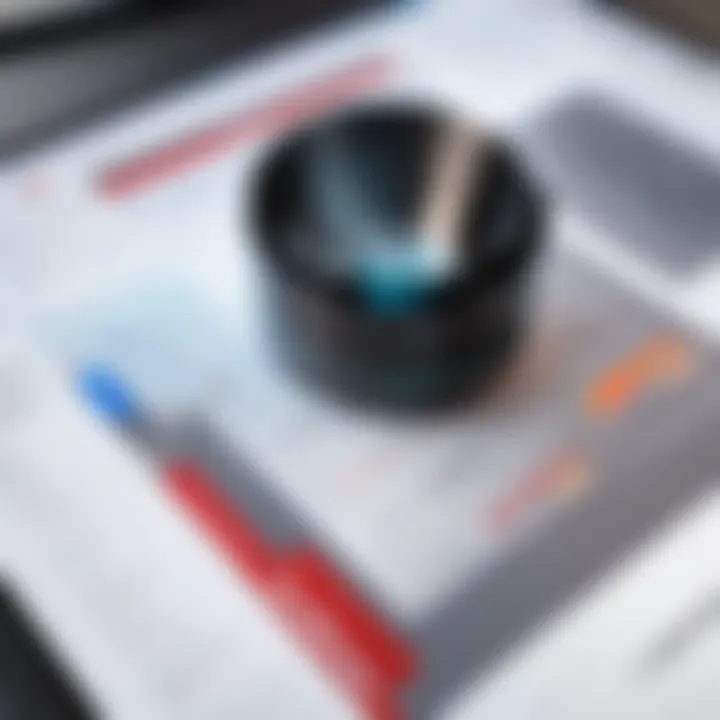
Hidden Costs in Implementation
Implementation of SolidWorks Simulation can bring some surprise costs that fly under the radar. For instance, after the initial purchase, other expenses may arise, including:
- Integration costs with existing systems: Sometimes, software won't play nice with older systems, requiring additional customization.
- Data migration expenses: Ensuring existing data transfers smoothly can take time and resources, affecting your timeline.
- Downtime during transition: There's often a learning curve, which can mean less productivity until your team is fully adept at using the new system.
Itโs prudent for organizations to thoroughly assess these hidden costs before diving in. A surprise expense here or there can quickly derail your budget.
Long-term Value Analysis
When all is said and done, a comprehensive long-term value analysis can shed light on whether SolidWorks Simulation is indeed worth the investment. Key factors to consider include:
- Efficiency in design processes: Gauge how much time the software saves versus manual design efforts.
- Cost of product failure: Assess the potential cost savings from simulating designs before physical prototypes are built and tested.
- Scalability: As your business grows, will the software grow with you without requiring a complete overhaul?
This analysis isn't merely an exercise in number crunching; it's about evaluating how well the software aligns with your strategic goals, fostering informed decision-making for future developments in the business.
"An ounce of prevention is worth a pound of cure." โ This adage rings true in SolidWorks Simulation decisions, where upfront understanding of costs can prevent larger headaches later.
Ultimately, managing the total cost of ownership well positions your company to leverage SolidWorks Simulation effectively and remains a crucial component of the larger financial planning process.
Comparative Analysis with Competitors
In today's fiercely competitive software market, understanding how SolidWorks simulation stacks up against its competitors is crucial for businesses aiming to optimize their engineering capabilities. Such analysis extends beyond mere numbers; it invokes a broader consideration of the features, costs, and overall value provided by different simulation tools. By slicing through the surface, companies can unearth insights that will enable them to not only save money but also bolster their design accuracy and innovation.
Competitor Pricing Models
Diving into competitor pricing models sheds light on how much organizations might expect to shell out when opting for alternatives to SolidWorks. When comparing prices, itโs essential to factor in not just the interface but also the functionality that comes with each tool.
For instance, ANSYS offers a versatile suite, but users often find it can be significantly pricier, especially when additional licenses or powerful modules are required. Another notable player, Autodeskโs Fusion 360, often follows a more affordable subscription model that appeals to small businesses and startups, promoting accessibility.
The effective pricing strategy should take into account the following:
- Base License Costs: The initial investment to get started with a software.
- Feature Add-ons: Additional fees for advanced capabilities.
- Maintenance Fees: Ongoing costs that may be factored into the total expenditure.
- User Scalability: Discounts offered for bulk licenses can dramatically influence the final cost.
Understanding these elements can make a notable difference when narrowing down options. Carefully considering how these pricing models align with budgetary constraints is an investment into a smarter decision-making process.
Feature Comparison with Alternatives
The heart of any solid comparative analysis lies within the features offered by the competing softwares. SolidWorks shines in many respects, yet knowing what you trade off when you select an alternative can be enlightening.
In terms of strength, Solidworks Simulation provides an expansive array of capabilities which include:
- Dynamic & Static Analysis: SolidWorks boasts robust solutions for both static and dynamic modeling.
- Parametric Design Tools: User-friendly tools for alterations and modifications.
- Real-time Simulation Feedback: An appealing feature that facilitates instantaneous adjustments in design.
Competing platforms, like COMSOL Multiphysics, provide certain unique features that may cater to specific sectors. Their ability to conduct simulations across multiple domains โ like structural, fluid, thermal all in one โ sets them apart. However, the interface can be less intuitive, leading to potentially longer learning curves, especially for newer engineers.
Moreover, integrating simulation capabilities within a broader suite of design tools may tip the scale towards an alternative tool. For instance, a user needing close collaboration between CAD and simulation may find value in apps like Altair HyperWorks.
Understanding these feature sets allows a business not only to assess immediate needs but to plan for future projects and expansion as well.
"In essence, making an informed decision about simulation tools can lead to not only cost savings but significant improvements in design efficiency and innovation."
Being informed allows for proactive choices that place businesses in a position of advantage.
Case Studies: Businesses Leveraging SolidWorks Simulation
Understanding how businesses utilize SolidWorks simulation provides invaluable insights into its practical benefits and economic advantages. Case studies offer concrete examples, demonstrating how companies improve their design processes, save on costs, and foster innovation through simulation tools. These real-world applications not only illuminate the versatility of SolidWorks but also illustrate the importance of investing in effective simulation technology. By examining different scenarios, it's clear that the ability to simulate designs before they reach production can significantly affect both the bottom line and the speed of development.
Cost Savings through Efficient Design Processes
In todayโs competitive landscape, businesses are constantly under pressure to enhance efficiency. SolidWorks simulation allows companies to model various design options early in the development stage. For instance, an automotive manufacturer utilized SolidWorks to simulate crash tests virtually rather than conducting expensive physical tests. This proactive approach led to significant cost reductions by minimizing material waste and shortening prototyping cycles.
- Reduced Prototyping Costs: Companies can experiment with numerous designs without incurring the costs associated with building each prototype.
- Faster Time-to-Market: Simulations help identify potential design flaws early on, allowing for quicker revisions and faster launch times.
- Material Efficiency: By virtually testing with different materials, businesses can identify the most effective ones, trimming unnecessary expenses.
Another example comes from the aerospace industry, where a major player used SolidWorks simulation to optimize components for weight and strength. This effort resulted in manufacturing lighter parts that increased fuel efficiencyโa cost-saving measure that reapplied across multiple projects.
Innovation and Risk Mitigation via Simulation
When companies embrace SolidWorks simulation, they are not just streamlining processes; they are also fostering innovation. By encouraging a culture of experimentation through simulation, businesses can safely explore out-of-the-box ideas and push the boundaries of conventional design.
- Safer Experimentation: With the ability to simulate various scenarios, companies can explore radical ideas without the associated risks of real-world testing.
- Improved Quality Control: Simulation allows organizations to better predict how their products will perform under real-world conditions, addressing potential failures before they happen.
- Informed Decision Making: With robust simulation data, teams are well-equipped to make strategic decisions about product development and feature enhancements.
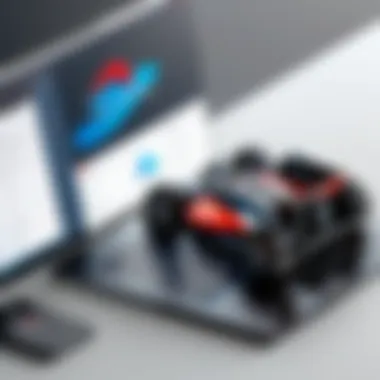
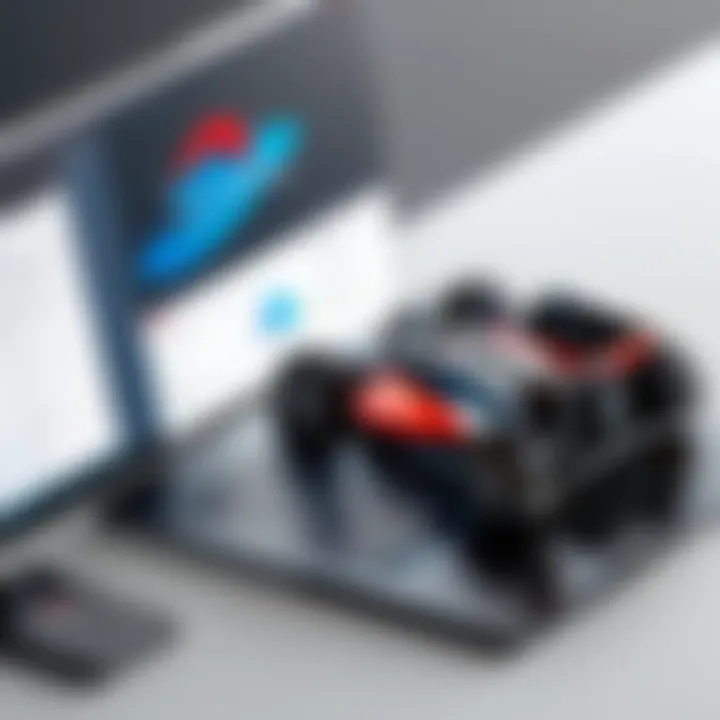
Consider the case of a tech startup specializing in consumer electronics. By employing SolidWorks simulation, they tested new device designs for thermal properties and mechanical stress. Their proactive risk assessments not only prevented costly failures post-launch but also cultivated a reputation for reliability in their product line.
"The use of SolidWorks simulation turned our design team into rapid innovators, allowing us to pivot quickly and maintain our technological edge in the marketplace."
โ Design Director at XYZ Electronics
Through these case studies, it's evident that leveraging SolidWorks simulation can lead to remarkable financial savings and foster a culture of innovation. By examining these examples, businesses can draw conclusions about their own operational strategies and consider how simulation tools might enhance their design and development processes.
Best Practices for Cost Management
Managing costs when utilizing SolidWorks Simulation can be a balancing act worthy of a seasoned juggler. The unique blend of software capabilities, associated training, and ongoing maintenance can quickly lead to financial headaches if not handled with care. By understanding best practices in cost management, companies can enhance their engineering outputs without breaking the bank.
Evaluating Software Needs vs. Budget
When contemplating costs, the first step is understanding the specific software needs of the organization. Too often, decision-makers might be swayed by flashy features that look appealing but do not fit practical requirements. Doing a thorough evaluation entails:
- Assessing current projects: Are they complex enough to require finite element analysis, or is basic simulation sufficient?
- Engaging team feedback: Involving engineers and designers ensures all voices are heard, which helps align software capabilities with real-world demands.
- Analyzing usage patterns: Previous projects can give clues as to the tools that actually made a difference. Look back at what simulations were run most frequently and why.
By setting clear criteria based on needs rather than desires, businesses can chart a course that aligns with budgetary constraints while still holding on to essential functionalities.
Negotiating Contracts and Pricing
Once a clear understanding of needs is established, the next step is honing skills for negotiation. Some businesses might bristle at the thought of negotiating contracts, considering it intimidating or time-consuming. However, these negotiations can produce significant savings if navigated smartly. Here are strategies to consider:
- Research competitor rates: Be aware of what similar software costs, and leverage this to fuel negotiations. This information can serve as a strong bargaining chip.
- Inquire about package deals: Often, software firms offer bundled pricing or discounts for multiple licenses. Understanding these can lead to figuring out a more favorable deal for your specific needs.
- Engage directly with providers: Utilize personal connections or social platforms to engage in discussions with software distributors. Sometimes, upon uncovering direct lines of communication, opportunities for bespoke arrangements can emerge.
Itโs all about approaching every conversation with clarity and readiness to articulate the organizationโs specific requirements. By drawing clear lines on budget alongside expected functionalities, cost-effective solutions can often be found.
"Effective negotiation starts with understanding both sidesโ needs."
By keeping these best practices in mind, companies can navigate the often murky waters of SolidWorks Simulation pricing with greater confidence and clarity. The cost of software shouldn't eclipse the value it brings. With strategic thought and careful decision-making, the right balance can be struck.
Future Trends in SolidWorks Simulation Pricing
Understanding the future landscape of SolidWorks simulation pricing is essential for professionals and businesses looking to invest wisely in engineering software. Staying abreast of upcoming trends ensures that organizations can leverage the most cost-effective solutions while maximizing their return on investment. Adapting to the evolving market dynamics is crucial as competition stiffens and technology progresses, shaping the way simulation tools are priced and marketed.
Impact of Cloud-based Solutions
The advent of cloud computing has revolutionized how software is delivered and priced. For SolidWorks simulation, this shift is not just a technical upgrade but also a pivotal moment for pricing strategies.
Cloud-based solutions offer numerous advantages, such as:
- Accessibility: Users can access their simulation tools from virtually anywhere, provided they have an internet connection. This removes traditional barriers of having to be in a specific location to run simulations.
- Scalability: Companies can easily scale their usage up or down based on project demands. Instead of purchasing extensive licenses for software they might not use consistently, businesses can adapt their cloud subscription according to need, which enhances efficiency and cost management.
- Cost Efficiency: While upfront costs might seem lower with cloud solutions, organizations often find that total expenses balance out or decrease in the long run due to reduced hardware requirements and maintenance.
Nevertheless, a cautionary note must be adhered to. Reliance on cloud solutions means increased exposure to potential cybersecurity risks. Itโs important for organizations to thoroughly vet their cloud providers to ensure robust data security measures are in place.
Evolving Market Dynamics and Pricing Structures
The landscape of SolidWorks simulation is continually shifting, influenced by various market forces. Understanding these dynamics helps businesses make informed choices regarding pricing models. A few factors impacting pricing structures include:
- Subscription Models: As more businesses lean towards subscription-based licenses, companies offering SolidWorks simulation might adjust their pricing strategies to match customer preferences.
- Competitive Pressure: With numerous simulation tools available, pricing strategies are often influenced by competitors. A new entrant or a price drop from a competitor can spur existing companies to reevaluate their pricing structures.
- Customer Feedback and Demand: The rise of user-driven development means that customer insights can dramatically shape features and pricing. Companies that listen and adapt to user-requested features might change pricing models to reflect added value or streamline options.
"Future trends are not just about whatโs next but how organizations can pivot to meet new demands effectively."
Additionally, as tech-savvy businesses invest more in simulation tools that integrate advanced technologies like artificial intelligence or machine learning, they might expect to incur higher costs. However, the trade-off often lies in tangible efficiencies or groundbreaking innovations in design capabilities that these advanced tools deliver. Navigating these evolving pricing structures will demand agility and foresight from businesses.
Closure
The conclusion of this article is pivotal in underscoring the importance of understanding SolidWorks simulation pricing. It's not merely about numbers; itโs about aligning technology with strategic business objectives. The insights provided can significantly influence how organizations approach their investment in simulation tools.
Weighing the Value of SolidWorks Simulation
When examining the value of SolidWorks Simulation, it becomes evident that this software offers more than a linear cost-benefit return. The advanced simulation capabilities can lead to significant cost savings in the product development process. By recognizing potential design flaws early on, businesses can avoid costly late-stage modifications.
- Enhanced design accuracy leads to superior products.
- Better resource allocation reduces waste.
- Improved time-to-market fosters competitive advantage.
Engaging with SolidWorks Simulation is, in many respects, an investment in future-proofing oneโs engineering processes. Companies that can adapt and innovate are those that sustain growth. Therefore, itโs crucial for decision-makers to quantify these benefits against the initial outlay. The comparison must not be restricted just to software costs but should also reflect the broader implications on product lifecycle and user training.
Informed Decision Making for Future Purchases
Informed decision making is essential when considering SolidWorks Simulation as part of a company's toolkit.
To guide financial allocation effectively, factors such as:
- Total Ownership Cost
- Required Features
- User Training needs
must be thoroughly evaluated. This kind of scrutiny ensures that the selection is not only fitting for current requirements but is also adaptable for future needs.
When stakeholders approach the purchasing process with a clear understanding of these elements, the outcome is often a well-rounded and justified investment.
Seeking clarity on simulation pricing can result in a more effective tool selection, empowering businesses to streamline their workflows successfully.