Unlocking Manufacturing Business Software: Insights & Trends
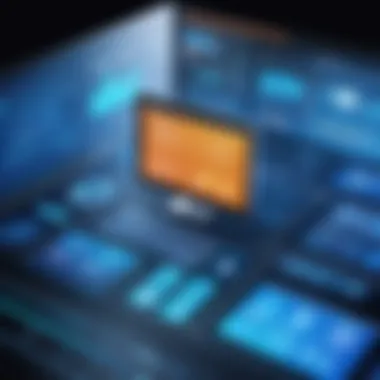
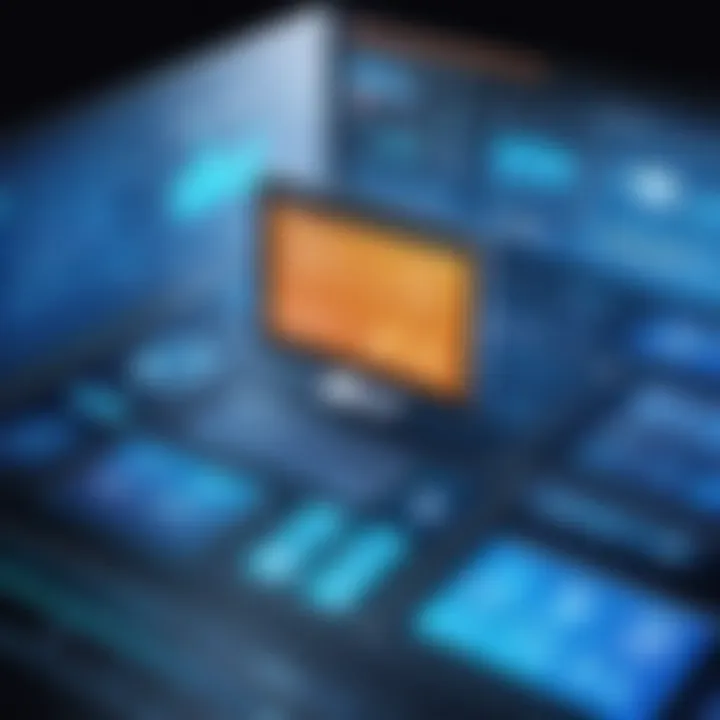
Intro
Manufacturing business software has become indispensable for companies striving to enhance their operational efficiency and make informed decisions. In an era where competition intensifies, effective software solutions can elevate a manufacturer's capabilities significantly. This article explores the various facets of these software solutions, from their core features to pricing models. Understanding the landscape of manufacturing software is crucial for decision-makers in choosing the right technology to suit their unique business needs.
Key Features
Overview of Features
Manufacturing business software typically encompasses several core features designed to streamline operations and improve productivity. These features include:
- Inventory Management: Keeping track of raw materials and finished goods.
- Production Scheduling: Planning and optimizing manufacturing processes.
- Quality Control: Ensuring the output meets the required standards.
- Supply Chain Management: Coordinating with suppliers and managing logistics effectively.
- Reporting and Analytics: Providing insights into performance and identifying improvement areas.
Each feature plays a critical role in ensuring the smooth running of manufacturing operations, ultimately contributing to enhanced efficiency.
Unique Selling Propositions
Manufacturing software offers distinct advantages that make it a necessity for many businesses. Key selling propositions include:
- Increased Efficiency: Automation of repetitive tasks reduces human error and speeds up processes.
- Data-Driven Decision Making: Real-time analytics help in making informed decisions promptly.
- Scalability: Software can be tailored to meet the evolving needs of growing businesses.
- Cost Reduction: By optimizing resources, manufacturers can lower operational costs significantly.
These unique advantages underscore the importance of investing in suitable manufacturing software to advocate for improvements in various aspects of the business.
Pricing Models
Different Pricing Tiers
The pricing structures for manufacturing software can vary greatly, influenced by feature set, scalability, and service levels. Common pricing models include:
- Subscription-Based: Monthly or yearly fees based on usage, allowing businesses to scale their software cost effectively.
- One-Time License Fee: A single payment for perpetual use, often favored by larger enterprises.
- Freemium Model: Basic functionality is offered for free, with premium features available for a fee.
Understanding the pricing models helps businesses assess their budget and align it with their operational needs.
ROI and Cost-Benefit Analysis
Before committing to any software, conducting a return on investment (ROI) analysis is essential. Considerations include:
- Initial Costs: Assess the upfront expenses related to software acquisition and implementation.
- Operational Savings: Estimate the potential savings generated through increased efficiency and reduced waste.
- Long-Term Benefits: Evaluate the software's role in sustaining growth and adapting to market changes.
Calculating ROI involves a detailed examination of both tangible and intangible benefits. This analysis supports manufacturers in making informed investments that align with their strategic business goals.
Overview of Manufacturing Business Software
In the modern landscape, manufacturing businesses face the necessity of integrating advanced technology to enhance operations. Manufacturing business software plays a crucial role in achieving these efficiencies. It serves as a backbone for optimizing processes, managing resources, and facilitating communication. An effective software solution can significantly affect decision-making, ultimately leading to improved productivity and financial performance.
Definition and Importance
Manufacturing business software is a suite of applications designed to help businesses streamline operations. Its core purpose is to automate, manage, and optimize manufacturing processes, which can include planning, production, inventory management, and quality control.
Understanding how these systems function is vital for decision-makers. The integration of such tools not only helps in tracking workflows but also provides analytics that support informed choices. In an environment where precision matters, the importance of accurate and real-time data cannot be overstated. Thus, these software solutions can lead to smarter operations and an agile response to market demands.
Historical Context
Historically, manufacturing relied heavily on manual processes which often resulted in delays and inaccuracies. The advent of manufacturing software began around the mid-20th century with basic automation tools. As technology evolved, so did manufacturing software. For example, the introduction of Enterprise Resource Planning (ERP) systems in the 1990s marked a significant transition. These systems allowed for a more cohesive approach to managing various domains within manufacturing.
Over the years, improvements in computing power and the internet led to the development of more sophisticated systems. Features like cloud computing and real-time analytics have reshaped how businesses operate. Each transition reflected a need for improvement, pushing forward the integration of software into everyday operations, directly influencing the pace at which modern manufacturing can adapt to changes in demand.
"Effective manufacturing business software is not just a luxury; it is a necessity for any competitive organization in today's global market."
As we move forward, understanding these historical shifts sheds light on current practices and helps predict future trends in manufacturing business software.
Categories of Manufacturing Software
The category of manufacturing software plays a vital role in the industry by enabling businesses to streamline their operations, improve efficiency, and adapt to changing market demands. Each category addresses specific needs and offers unique functionalities. When exploring manufacturing software, decision-makers must understand the different categories to select the right tools that align with their organizational goals.
Enterprise Resource Planning (ERP)
Enterprise Resource Planning, commonly known as ERP, serves as the backbone of manufacturing operations. This software integrates various business processes into one comprehensive system. The integration allows for better data flow between finance, procurement, production, and sales departments. By using ERP, manufacturers can achieve centralized data management, which leads to informed decision-making.
Furthermore, ERP solutions often include modules tailored to the manufacturing industry, such as production planning, inventory management, and compliance reporting. Notably, they can enhance resource planning and optimization, resulting in reduced waste and increased productivity.
Manufacturing Execution Systems (MES)
Manufacturing Execution Systems act as a bridge between the shop floor and higher-level enterprise systems. MES provides real-time data about production processes. This includes tracking work-in-progress, monitoring equipment performance, and managing labor efficiency.
The ability to capture real-time data helps manufacturers respond swiftly to issues as they arise. This leads to improved production consistency and quality. Moreover, these systems enhance traceability across production lines, which is crucial for compliance and quality control.
Supply Chain Management (SCM)
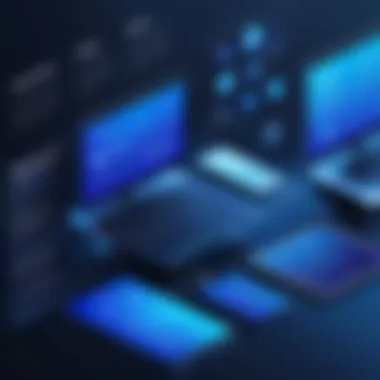
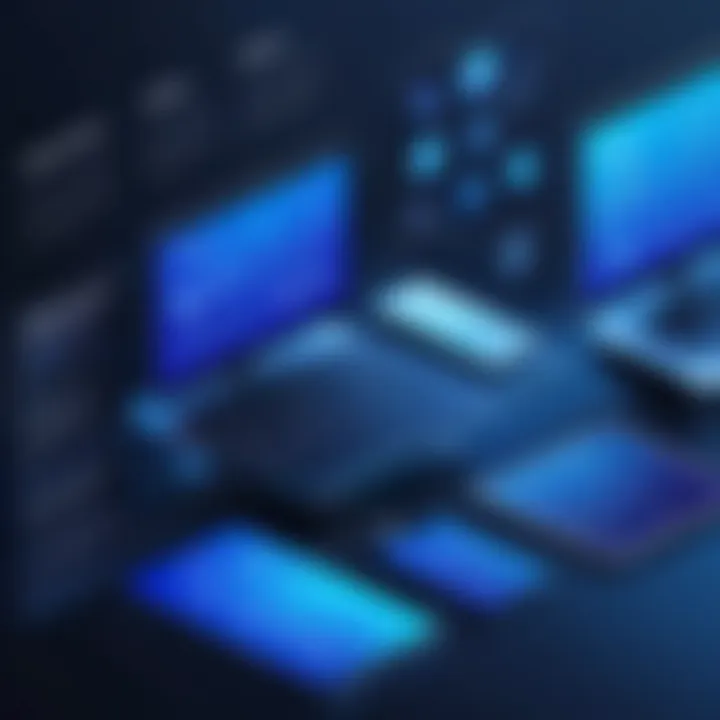
Supply Chain Management software focuses on optimizing the flow of goods and services from suppliers to customers. The aim is to enhance the entire supply chain, from procurement to distribution.
SCM systems facilitate better inventory tracking, demand forecasting, and supplier collaboration. This leads to improved lead times and cost management. Effective SCM also enables manufacturers to react quickly to market changes, thereby increasing competitiveness.
Product Lifecycle Management (PLM)
Product Lifecycle Management software manages a product's life from inception to retirement. This includes design, manufacturing, service, and disposal phases.
PLM enables collaboration among various teams, promoting innovation and reducing time-to-market. It provides a centralized repository for product data, ensuring that all stakeholders have access to the latest information. The effective use of PLM can lead to better product quality and customer satisfaction.
Understanding these categories is essential for manufacturers to invest in the right technologies. Each category brings specific benefits and challenges, thus necessitating a tailored approach based on individual business needs.
Key Features of Manufacturing Software
Understanding the key features of manufacturing software is essential for any organization seeking to enhance its operations. These features serve as the backbone of any software solution, ensuring that it meets the specific needs of the manufacturing environment. When evaluating software, decision-makers must consider elements such as efficiency, scalability, and reliability. The effectiveness of the software often hinges on its ability to provide tools that improve productivity and enable informed decisions.
Real-Time Data Analytics
Real-time data analytics is a crucial feature of manufacturing software. It provides organizations with immediate insights into their operations, allowing for timely adjustments. For instance, companies can track production metrics instantaneously, revealing inefficiencies as they occur. This immediacy can lead to quicker responses to production downtime or quality issues, ultimately saving time and resources.
Organizations using real-time analytics reported significant improvements in performance. For example, when implementing a system with advanced data analysis capabilities, a manufacturer might reduce its production downtime by up to 20%. Such metrics underscore the advantage of utilizing real-time data in decision-making processes.
Integration Capabilities
Another vital feature is integration capabilities. Manufacturing environments often consist of various software tools and systems. A robust software solution must integrate seamlessly with existing systemsβsuch as Enterprise Resource Planning (ERP) and Customer Relationship Management (CRM) systems. Effective integration facilitates smooth data flow between departments, which enhances collaboration and coordination.
Furthermore, integrated systems can streamline processes and reduce human error. When using multiple systems, the potential for data silos exists, leading to inconsistencies. A manufacturing software that promotes integration minimizes these issues, improving overall operational efficiency.
Automation and Control
Automation and control functionalities play a significant role in modern manufacturing software. Automating repetitive tasks can enhance productivity and free employees to focus on more critical aspects of their roles. For instance, automation can manage scheduling, inventory control, and quality checks with minimal human intervention.
Control features also allow manufacturers to monitor operations closely. With the ability to adjust parameters in real time, businesses can optimize processes and maintain quality standards. This level of control becomes paramount in high-stakes manufacturing sectors, where products must meet strict regulatory requirements. By employing automation, companies can maintain consistency and reliability while reducing operational risks.
Compliance and Reporting
Compliance and reporting are necessary features of any manufacturing software. Regulatory requirements dictate that manufacturers adhere to strict guidelines to ensure product safety and quality. Software solutions must include comprehensive reporting capabilities to monitor compliance effectively.
With automated reporting features, manufacturers can generate reports quickly and accurately. This capability reduces the time spent on documentation while increasing accuracy. Regulatory bodies often require detailed records, and an effective software solution can facilitate this need without placing an undue burden on the workforce.
Achieving compliance through an integrated software system can significantly minimize risks and enhance credibility with customers and regulators alike.
In summary, the key features of manufacturing software play a critical role in driving efficiencies and ensuring effective decision-making. Each featureβfrom real-time data analytics to compliance reportingβcontributes to a more streamlined manufacturing process.
Benefits of Manufacturing Business Software
In the competitive landscape of manufacturing, selecting the right software solution is pivotal. Manufacturing business software plays a crucial role not only in streamlining processes but also in catalyzing growth. Understanding its benefits is essential for decision-makers aiming to leverage technology for operational excellence. Employing such software enables businesses to thrive by enhancing various facets, like efficiency, cost management, and product quality.
Increased Efficiency
Efficiency is often the foremost concern in manufacturing. Implementing a robust business software system can lead to improved workflow and higher productivity levels. Automated processes reduce manual tasks, allowing staff to focus on more strategic activities. For instance, inventory management systems can provide real-time data on stock levels, minimizing downtime caused by shortages or excess inventory.
In addition, integration capabilities with existing systems facilitate seamless data flow. When all departments from production to sales are connected, it promotes a unified approach to operations. This real-time connectivity aids in faster decision-making and adaptability to changes in market demand. By embracing these technologies, organizations can realize enhanced operational efficiency and quicker response times.
Cost Reduction
Another significant advantage of manufacturing business software is its potential to drive cost savings. By streamlining operations and reducing waste, businesses can significantly lower their operational costs. For example, predictive maintenance features can prevent machinery breakdowns, mitigating the costs associated with repairs and downtimes. This control over expenses contributes to overall profitability.
Moreover, data analysis tools enable better forecasting and resource allocation. When companies can predict demand more accurately, they can optimize their supply chain and manage inventory more effectively. This functionality minimizes waste and ensures resources are utilized efficiently. Consequently, cost reduction becomes not just possible but achievable through systematic recalibration of business processes.
Improved Quality Control
In manufacturing, quality is paramount. Implementing business software that includes robust quality control features can lead to significant improvements in product standards. Automated tracking systems can monitor production practices, ensuring compliance with industry regulations. This level of oversight helps in identifying defects early, thereby minimizing waste as well as customer complaints.
Utilizing data analytics to assess quality trends can also reveal insights about manufacturing processes. Companies can track performance metrics and spot inconsistencies, making it easy to implement preventative measures. Therefore, advanced quality control functionalities ensure that companies uphold their commitments to providing top-tier products.
Enhanced Collaboration
Collaboration within an organization is vital for driving innovation and achieving goals. Manufacturing business software fosters enhanced collaboration among teams. By centralizing communication and sharing project updates in real time, these tools dismantle departmental silos.
Moreover, cloud-based solutions allow for remote access to data and project management systems. This flexibility supports teamwork across different locations and time zones. Furthermore, incorporating collaborative tools ensures that individuals can contribute their expertise, leading to better problem-solving and innovative solutions. Hence, fostering a culture of collaboration is a direct benefit of employing effective manufacturing business software solutions.
Challenges in Implementation
Implementing manufacturing business software can present various hurdles that organizations must navigate. Understanding these challenges is crucial for decision-makers as they look to enhance their operational capabilities. Addressing implementation challenges not only ensures smoother transitions but also leads to better overall outcomes when integrating new systems.
Change Management
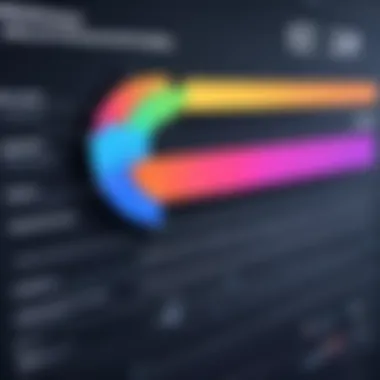
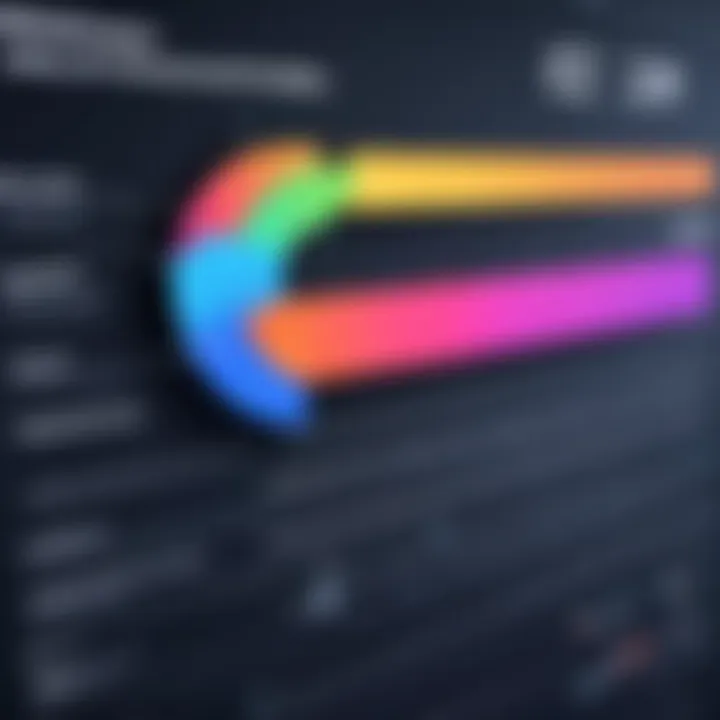
Change management is a critical aspect when implementing new software in any organization. The transition from existing processes to new ones requires not just technical adjustments but also cultural shifts within the workforce. Employees might resist change due to fear of the unknown or concerns about increased workloads. For manufacturing businesses, where routines are often well-established, this resistance can significantly hinder progress.
To address change management effectively, organizations should focus on several key strategies:
- Communication: Clearly articulate the benefits of the new software. This can include improved productivity, reduced errors, and enhanced data management.
- Training: Offering comprehensive training sessions helps staff feel more confident in using the new system, thus easing the transition.
- Support Systems: Establishing a support system where employees can seek help during the initial stages of adoption can alleviate anxiety and reinforce positive engagement with the new technology.
Handling change management thoughtfully can minimize disruptions and enhance the acceptance of the new software across the organization.
Data Migration Issues
Data migration is another considerable challenge when implementing new manufacturing business software. Moving vast amounts of data from legacy systems to new platforms often involves several difficulties. This mainly involves ensuring data accuracy, completeness, and integrity throughout the transition.
Here are some key considerations regarding data migration:
- Data Quality Assessment: Prior to migration, a thorough evaluation of existing data is essential. This includes identifying any data that is outdated, redundant, or irrelevant.
- Mapping Data Fields: Understanding how data from the old system corresponds to the new system is vital. This mapping process often requires careful planning.
- Testing Migration Processes: Conducting preliminary tests with subsets of data can help identify potential issues before full-scale migration, allowing for adjustments.
Overall, tackling data migration issues head-on can prevent future headaches related to data integrity, which can severely impact operations.
Integration with Existing Systems
Integration with existing systems is also a significant barrier during software implementation. Organizations often have a range of legacy systems that must interact with the new manufacturing software. This integration is critical to ensure seamless workflows and consistent data sharing across platforms.
Consider these important factors when approaching integration challenges:
- Compatibility: Assess whether the new software is compatible with existing systems. Some older systems may require updates or middleware solutions to function effectively with newer technology.
- API Development: Building application programming interfaces (APIs) can facilitate smoother communication between systems, allowing for more efficient data exchange and collaboration.
- Continuous Monitoring: Post-integration, it is essential to regularly monitor system interactions to identify and rectify any issues that may arise. This allows for continuous improvements in performance and productivity.
By prioritizing integration during the implementation phase, organizations can create a unified technological ecosystem that supports their manufacturing objectives.
Factors Influencing Software Selection
Selecting the right manufacturing business software is a complex decision. Several factors directly influence this process. These elements determine not only the functionality and effectiveness of the software but also ensure it aligns with the companyβs overall objectives. Understanding these factors helps organizations tailor their selection process efficiently, thus maximizing return on investment.
Business Size and Industry
The size of a business and the specific industry it operates in plays a critical role in software selection. Large corporations have different needs than small or mid-sized companies. For instance, a multinational manufacturer might require extensive features that can handle various operations across multiple locations. In contrast, a startup might prioritize simplicity and cost-effectiveness.
Each industry may also have unique requirements. For instance, the automotive sector often needs software that complies with strict safety regulations. In this case, the software must incorporate compliance features and a focus on quality control.
- Large enterprises may look for systems with robust integration capabilities.
- Smaller companies might prioritize user-friendly interfaces and affordability.
In essence, matching the softwareβs capabilities with the organizationβs size and sector is crucial for optimal functioning.
Budget Constraints
Budget constraints are a fundamental consideration when selecting manufacturing software. Organizations must evaluate their overall financial health and determine how much they can realistically invest in new technology. High costs could stem from licensing fees, implementation efforts, and ongoing maintenance.
Cost-effectiveness does not mean compromising quality. Many solutions, including open-source options, can provide the necessary features without burdening the company financially. Prioritizing features based on immediate needs can also help manage costs effectively.
Some strategies to manage budget constraints include:
- Prioritizing Essential Features: Identify which functionalities are vital and which ones can be added later.
- Exploring Payment Plans: Many vendors offer various payment options that can ease upfront costs.
Engaging in diligent research and possibly negotiating with vendors can provide pathways to acquire software that fits within a budget without sacrificing value.
Scalability Requirements
Scalability is another critical factor in software selection. As organizations grow, their software should adapt accordingly. A manufacturing firm that anticipates expansion will benefit from solutions capable of accommodating increased operations. This includes the ability to handle more users, processes, and data.
Selecting scalable software can save a company significant time and resources over the long term.
Considerations here include:
- Future Needs Assessments: Analyze expected growth and ensure the chosen software can handle such transitions.
- Cloud Computing Options: Many modern solutions are cloud-based, allowing for easy adjustments as business demand changes.
Understanding scalability ensures that companies invest in systems that do not become obsolete quickly and can grow alongside their operations.
"Choosing software with scalability in mind can prevent companies from being forced into costly replacements as they expand."
In summary, thoughtful consideration of business size, budget limitations, and scalability requirements can help organizations make informed decisions about manufacturing software that align seamlessly with their operational needs.
Future Trends in Manufacturing Software
The landscape of manufacturing business software is evolving rapidly. Understanding these trends is essential for decision-makers in the field. Embracing innovations like artificial intelligence and cloud-based solutions can greatly enhance operational efficiencies. This section explores several key trends that are reshaping the fabric of manufacturing software.
Artificial Intelligence Integration
Artificial intelligence is not just a buzzword; itβs a significant component in the future of manufacturing software. AI can analyze vast amounts of data quickly, enabling businesses to make data-driven decisions. AI applications in manufacturing include predictive maintenance, quality control, and demand forecasting.
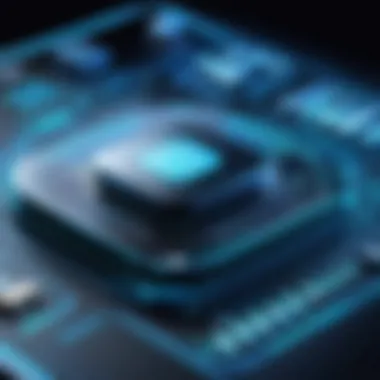
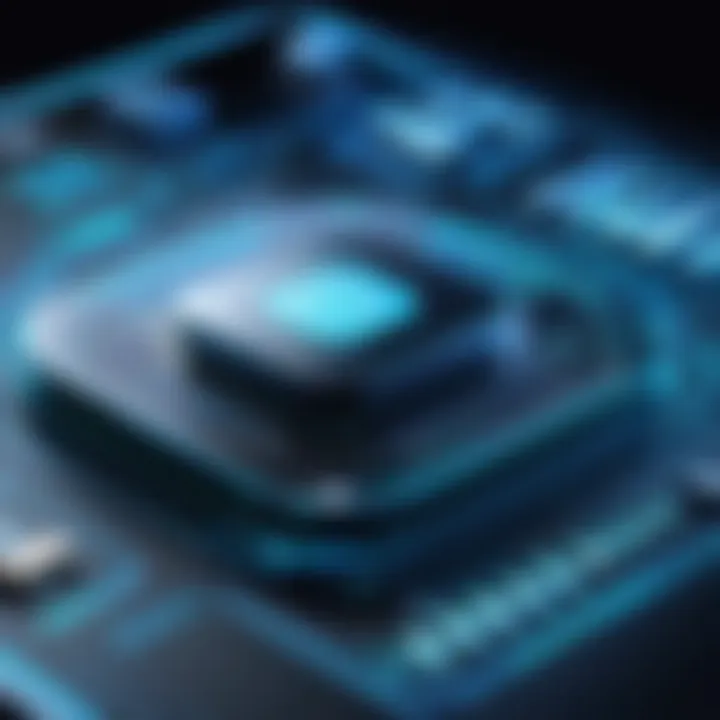
The benefits of integrating AI into manufacturing software include:
- Enhanced Decision-Making: AI analyzes historical data and trends, providing valuable insights.
- Increased Efficiency: Automation of routine tasks frees up human resources for higher-level strategic planning.
- Cost Savings: Reduction in errors and waste leads to lower operational costs.
Moreover, AI can help companies adapt to changing market conditions. By using machine learning algorithms, organizations can refine processes and improve product offerings based on real-time analytics.
Internet of Things (IoT) Adoption
The Internet of Things is fundamentally changing how manufacturers collect and analyze data. IoT devices can monitor equipment and processes, providing real-time feedback. This connectivity leads to smarter factories where machines and systems communicate seamlessly.
Key considerations regarding IoT adoption include:
- Data Collection: Constant monitoring generates valuable data that can inform decision-making.
- Operational Efficiency: Real-time monitoring helps in identifying bottlenecks and optimizing production flow.
- Predictive Maintenance: IoT can be used to schedule maintenance before breakdowns occur, saving time and costs.
As manufacturers adopt IoT, they must address security issues. Protecting sensitive operational data is crucial to preventing breaches that could disrupt operations.
Cloud-Based Solutions
Cloud-based solutions are transforming the delivery and management of manufacturing software. These platforms offer scalability, flexibility, and accessibility. By moving to the cloud, companies can ensure that they have the latest software without the hassle of local installations.
Benefits of cloud-based solutions include:
- Cost Efficiency: Reduces the need for expensive hardware and IT resources.
- Collaboration: Teams can access information from anywhere, promoting collaboration across departments and locations.
- Automatic Updates: Cloud services often include regular updates, ensuring that users always have access to the latest features and enhancements.
Businesses considering cloud solutions should evaluate their provider's security measures. Ensuring data protection and compliance with industry standards is critical for maintaining operational integrity.
"The future of manufacturing software hinges on how well organizations can adapt to these technological advancements. AI, IoT, and cloud solutions are not merely options; they are necessities for success in modern manufacturing."
As the manufacturing sector continues to evolve, being proactive in understanding these trends will provide a significant advantage. Adapting to emerging technologies can improve productivity and allow for innovation within industries.
Case Studies of Successful Implementations
Case studies of successful implementations provide an invaluable resource for organizations considering the adoption of manufacturing business software. These studies highlight real-world examples where businesses have effectively utilized software solutions to address challenges and improve operational efficiency. Analyzing these cases allows decision-makers to grasp the practical implications and benefits of various software options.
Insights gleaned from case studies often cover numerous aspects including implementation strategies, encountered obstacles, and the measurable impact of the software on business performance. Organizations can learn not only from the successes but also from the mistakes made during the adoption process. This level of understanding is critical in making informed decisions regarding software solutions that best fit specific business needs.
"Real-world results speak volumes louder than projections on paper. Before committing to a system, explore those who walked the same path."
Large Enterprises
Large enterprises often face complex operational challenges requiring sophisticated manufacturing business software. Case studies in this category typically emphasize the full-scale integration of Enterprise Resource Planning (ERP) systems, which enable cohesive management across various departments. For instance, a global automotive manufacturer adopted SAP S/4HANA to synchronize production planning with inventory management. The outcome included reduced lead times, more accurate demand forecasting, and enhanced production visibility.
Such implementations show the critical role of robust software in achieving scalability and organizational alignment. Moreover, the agility provided by a comprehensive system allows large corporations to adapt rapidly to market fluctuations. The lessons learned from these examples underscore the necessity for thorough change management and staff training to maximize the software's potential.
Mid-Sized Businesses
Mid-sized businesses frequently operate with tighter budgets and fewer resources than their larger counterparts, making efficient use of manufacturing software all the more vital. In numerous case studies, mid-sized manufacturing firms have shown significant gains by utilizing tailored solutions. For example, a medium-sized electronics manufacturer adopted a Manufacturing Execution System (MES) to streamline operations on the shop floor. By investing in this specific software, they improved real-time data collection, which facilitated better decision-making.
These case studies illustrate that even mid-sized organizations can achieve substantial productivity improvements. Key considerations often include alignment with existing systems and gradual integration, which minimizes disruption. Furthermore, learning from the experiences of similar-sized companies can inform better choices tailored to unique operational needs.
Startups and Small Companies
Startups and small companies present a different set of challenges and opportunities when it comes to manufacturing business software. Often characterized by limited budgets and resources, these organizations need versatile solutions that can grow with their business. A noteworthy case study involves a startup in the food manufacturing sector that implemented QuickBooks Enterprise to manage production costs and inventory. This investment allowed them to track every ingredient and reduce waste, leading to increased margins.
Such examples demonstrate that even the smallest firms can leverage software solutions to cultivate operational efficiency. Case studies in this category emphasize the significance of flexibility and customization in software choices. Startups can benefit from cloud-based solutions that enable scalability without heavy initial investments, paving the way for future growth.
Evaluating Vendor Solutions
Evaluating vendor solutions is a crucial stage in the process of implementing manufacturing business software. The complexity of this selection process, combined with the potential impact on operational efficiency, makes it imperative for decision-makers to take a systematic approach. A proper evaluation can lead to significant improvements in productivity, quality, and cost management while aligning technology with business objectives.
Market Research Techniques
Effective market research is essential to identify suitable software vendors. Techniques for market research include:
- Industry Reports: Review specific reports focused on manufacturing technology, which often highlight vendor capabilities.
- Online Surveys and Polls: Conduct surveys within industry circles to gather opinions and insights about various vendors. You may consider platforms like Reddit for forums where professionals discuss their experiences.
- Networking and Conferences: Attend industry conferences and seminars to engage directly with vendors and gather feedback from peers about vendor reputations.
By utilizing these techniques, businesses can narrow down software vendors that meet their specific manufacturing needs.
User Feedback and Reviews
User feedback and reviews serve as vital resources in evaluating potential software solutions. Understanding the real experiences of other users helps in making an informed choice. Some key areas to focus on include:
- Reputation: Look for vendors with a strong history of reliability and customer satisfaction.
- Functionality: Assess how the software has performed in practice. Specific case studies can reveal how the software has been implemented successfully in similar enterprises.
- Support Services: Evaluate the quality of customer support. Poor post-implementation support can lead to long-term operational challenges.
Gathering diverse viewpoints from users aids in building a well-rounded understanding of each vendor's offering.
Demo and Trial Periods
A practical step in evaluating vendor solutions includes requesting demos or trial periods. This hands-on experience allows companies to see the software in action and determine if it meets their expectations and requirements. Important aspects to consider during demo periods include:
- User Interface and Usability: Assess whether the software is intuitive and user-friendly. A complicated user interface can lead to increased training time and resistance from staff.
- Key Features: Take note of whether the software includes essential features that cater to manufacturing-specific needs such as inventory management and forecasting.
- Integration Capabilities: Evaluate how well the new software can integrate with existing systems. Limited compatibility can lead to additional issues down the line.
In summary, evaluating vendor solutions is a multi-faceted endeavor, encompassing rigorous market research, user feedback, and practical demonstrations. By employing these strategies, manufacturers can choose a software vendor that not only meets their current requirements but also supports future growth and adaptability.