Good Inventory Management: Maximizing Efficiency and Effectiveness
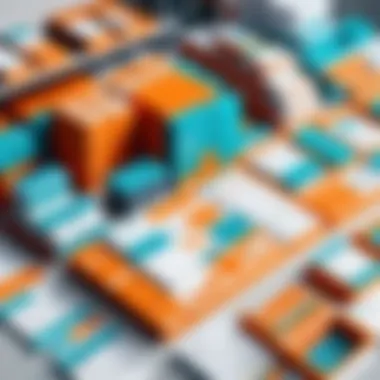
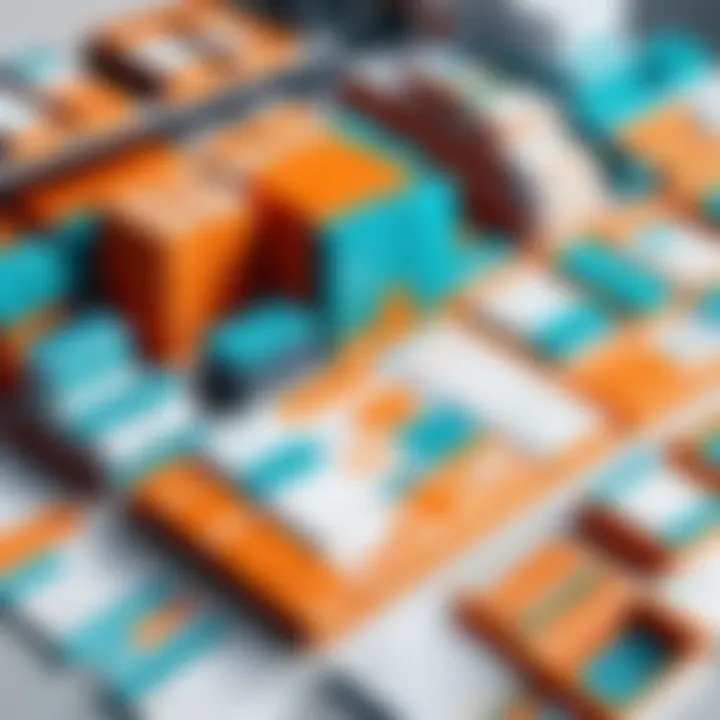
Intro
Good inventory management is crucial in todayโs business landscape. It serves as the backbone of supply chain operations, influencing operational efficiency, cost savings, and customer satisfaction. Businesses that implement sound inventory practices can respond to market demands effectively while minimizing excess stock and waste. This article will delve deep into strategies for maximizing efficiency and effectiveness in inventory management. Throughout the following sections, readers will learn about key features, unique selling propositions, pricing models, and the integration of data analytics into these practices.
"Effective inventory management not only supports a business's operational needs but also enhances its competitive positioning in the market."
In this guide, we will provide an overview of essential inventory management features and tools that can help businesses streamline processes. From understanding inventory cycles to the impact of data-driven decision making, each aspect contributes significantly to achieving optimal performance.
Through careful exploration, we aim to illustrate how effective inventory management is not just a necessity but a strategic advantage for any business looking to thrive.
Understanding Inventory Management
Inventory management sits at the heart of operational efficiency for any business. It encapsulates the process of overseeing the ordering, storage, and use of materials, and it plays a crucial role in maintaining the balance between supply and demand. The implications of proper inventory management reach far beyond just maintaining stock levels; it directly influences productivity, cost efficiency, and customer satisfaction.
Effective inventory management shapes the framework through which businesses can minimize their holding costs while maximizing the availability of products to meet customer demand. A clear grasp of this subject enables organizations to avoid pitfalls such as overstocking, which ties up capital unnecessarily, and stockouts, which can frustrate customers and lead to lost sales. Importantly, understanding inventory management fosters agility in operations, ensuring that businesses can adapt promptly to market fluctuations and consumer preferences.
Definition and Importance
Inventory management can be defined as the systematic approach to sourcing, storing, and selling inventory, including the management of raw materials, work-in-progress items, and finished products. Effective inventory management helps businesses maintain optimal stock levels, which reduces waste and enhances cash flow.
This practice is not merely an operational necessity; it is foundational to sustainable business success. Firms that optimize their inventory processes can benefit from improved profit margins due to fewer surplus goods and reduced operational costs. Furthermore, in today's increasingly competitive market, where consumers expect quick fulfillment of their orders, a robust inventory management framework can serve as a differentiator that enhances customer loyalty.
Key Objectives of Inventory Management
Several core objectives guide effective inventory management:
- Minimize Costs: Keeping inventory costs under control prevents the unnecessary drain of financial resources. Businesses should target optimal stock levels that align with demand while reducing storage and depreciation costs.
- Enhance Service Levels: By ensuring products are available when customers need them, companies can improve customer satisfaction and foster loyalty. This balance can help minimize backorders and missed sales.
- Streamline Operations: Efficient inventory management contributes to smoother operational workflows. Processes such as receiving, storing, and fulfilling orders become streamlined, leading to increased productivity.
- Facilitate Decision-Making: Accurate inventory records provide vital data for making informed business decisions. Analyzing inventory data can reveal trends that help optimize purchasing and production strategies.
- Mitigate Risks: Effective inventory management allows businesses to identify potential risks earlier, from supply shortages to shifts in consumer demand. This foresight enables proactive risk management strategies.
"The right inventory management approach can make the difference between thriving and merely surviving in todayโs market."
In summary, comprehending the fundamentals of inventory management is indispensable for any business aiming to operate at peak efficiency and effectiveness.
Types of Inventory
Understanding the various types of inventory is essential for effective inventory management. Each category plays a unique role in the overall supply chain and has specific implications for cost, quality, and efficiency. Failing to manage these types accurately can lead to financial implications and increased operational risks. By classifying inventory into distinct categories, businesses can implement targeted strategies to optimize inventory levels, reduce waste, and improve responsiveness to market demands.
Raw Materials
Raw materials form the foundation of any production-based business. These are the essential inputs used to create finished goods. Effective management of raw materials is crucial because it not only impacts the production process but also affects overall operational costs. A company must ensure that it maintains optimal quantities of raw materials to avoid production delays or excess stock. Overordering can lead to increased storage costs or spoilage, especially for perishable goods.
A Lean inventory approach can help minimize waste related to raw materials. Businesses can operate with a smaller amount of stock by precisely forecasting demand and aligning supply accordingly. However, demand forecasting is not always straightforward, and external factors, such as market trends or economic shifts, can disrupt forecasts.
Work-in-Progress (WIP)
Work-in-Progress inventory refers to items that are in the manufacturing process but are not yet complete. Managing WIP effectively is vital; it ties up cash but is necessary for maintaining a smooth production flow. High levels of WIP can indicate bottlenecks in production processes and lead to inefficiencies.
To optimize WIP, businesses should consider lean manufacturing principles and continuous improvement strategies. Set up systems for tracking the status of items in production to ensure a consistent flow. This visibility into the WIP can help identify areas where the production process can be streamlined or improved.
Finished Goods
Finished goods are products that are ready for sale. They represent the final stage in the supply chain process and are critical for meeting customer demand. Managing finished goods inventory entails balancing the right amount of stock to satisfy sales without overstocking. Too much finished goods inventory can lead to increased holding costs and potential markdowns if the products do not sell as anticipated.
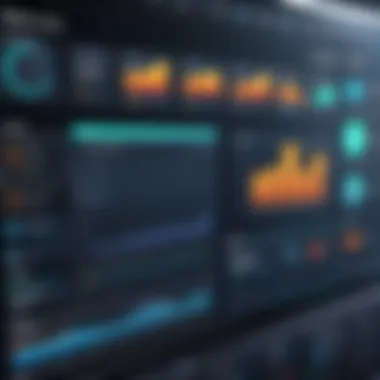
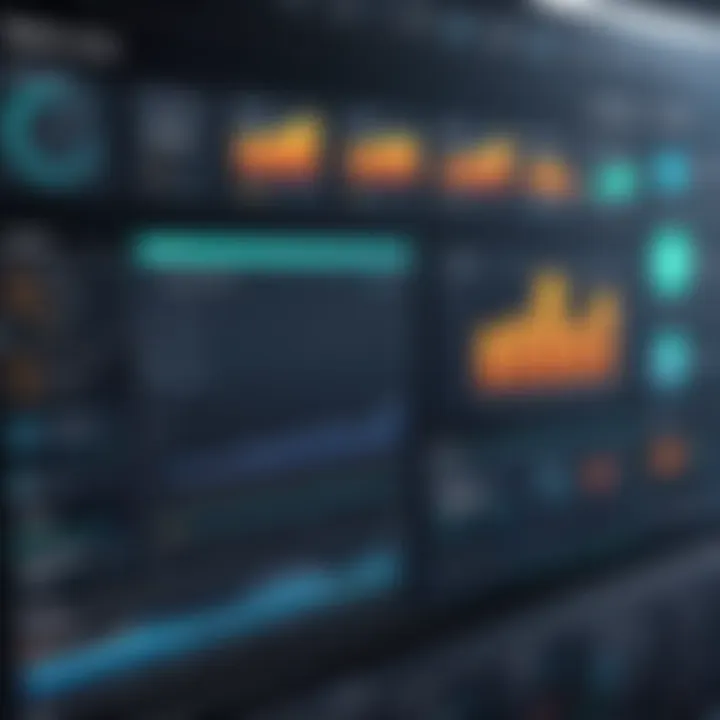
In the realm of inventory management, establishing reorder points is important. Companies should utilize historical sales data and market analysis to make informed decisions on how much inventory to keep on hand. This approach minimizes the risk of stockouts, which can lead to missed sales opportunities, while also preventing excess inventory.
MRO Supplies
Maintenance, Repair, and Operations (MRO) supplies are essential for sustaining production equipment and operational efficiency. These items, while often overlooked, play a vital role in keeping the production process running smoothly. If MRO supplies are inadequately managed, it can result in unexpected downtime and increased operational costs.
A proactive management approach is necessary for MRO inventory. This includes regular audits and inventory checks to ensure essential supplies are available when needed. Establishing relationships with multiple suppliers can also help ensure quick replenishment when required, further minimizing the risk of operational disruptions.
By understanding the different types of inventory, businesses can develop tailored strategies to manage each category effectively, leading to improved efficiency and reduced costs.
Inventory Management Techniques
Efficient inventory management is crucial for businesses aiming to optimize operations while minimizing costs. The implementation of specific inventory management techniques can lead to significant improvements in efficiency and effectiveness. These techniques guide decision-makers in maintaining optimal stock levels, reducing waste, and ensuring a smooth workflow across the supply chain.
Just-in-Time (JIT) Approach
The Just-in-Time (JIT) approach focuses on reducing inventory levels by receiving goods only as they are required in the production process. This technique minimizes holding costs and reduces the risk of overstocking. Companies like Toyota pioneered this method, demonstrating how effective it can be in improving cash flow and responsiveness to market demand.
A key benefit of JIT is that it enables manufacturers to increase efficiency in their operations, leading to lower operational costs. However, companies must have reliable suppliers and robust production schedules to implement this approach successfully.
ABC Analysis
ABC Analysis is a classification technique that categorizes inventory items into three groups based on their importance and value.
- A Items: High-value items with a low frequency of sales.
- B Items: Moderate value items with a moderate frequency of sales.
- C Items: Low-value items with a high frequency of sales.
This classification helps businesses prioritize their inventory management efforts. By focusing on A items, companies can enhance control and optimize stock levels, ensuring that essential products are always available. Understanding the significance of each category can lead to informed decision-making and improved resource allocation.
Economic Order Quantity (EOQ)
The Economic Order Quantity (EOQ) model calculates the ideal order quantity that minimizes total inventory costs, which includes ordering, holding, and stockout costs. This technique helps businesses determine when to reorder and how much to stock, optimizing inventory levels while balancing costs.
The EOQ formula is useful for small to medium-sized businesses where demand is steady. Applying EOQ can significantly reduce overall inventory costs. However, changes in market demand or unexpected disruptions can affect the accuracy of calculations and necessitate re-evaluation.
Dropshipping
Dropshipping is an inventory management approach where retailers do not keep goods in stock. Instead, they transfer customer orders to a third party, which then ships the products directly to the customer. This model reduces the need for extensive warehousing and allows businesses to offer a broader product range without the associated costs.
However, dropshipping has its challenges. Retailers must maintain strong supplier relationships and ensure timely fulfillment. Additionally, reliance on third parties can lead to potential supply chain vulnerabilities. Despite these drawbacks, many startups and small businesses find dropshipping an attractive entry point into e-commerce.
By understanding and applying these inventory management techniques, businesses can enhance their operational processes. Each method has unique benefits and challenges, but when implemented correctly, they can create a streamlined approach to managing inventory effectively.
Technology in Inventory Management
In the realm of inventory management, technology serves as a cornerstone for improving efficiency and effectiveness. As businesses strive to optimize their operations, leveraging technology becomes critical. Advanced tools not only streamline processes but also offer data-driven insights that guide decision-making. The implementation of these technologies can lead to a significant reduction in operational costs and better customer service.
Inventory Management Software
Inventory management software is essential for tracking stock levels, orders, and deliveries. Modern software solutions offer real-time visibility into inventory status, which helps businesses maintain optimal stock levels. Such systems come with various features including automated order processing and reporting capabilities. Implementing this software can reduce human error and speed up the inventory management process.
Several leading software solutions are available today. For instance, platforms such as TradeGecko and Fishbowl Inventory offer user-friendly interfaces and robust reporting tools. These tools are designed to cater to various business sizes and industries. Businesses must assess their specific needs before choosing software, as selecting the wrong tool can create inefficiencies rather than solve them.
Barcode and RFID Technology
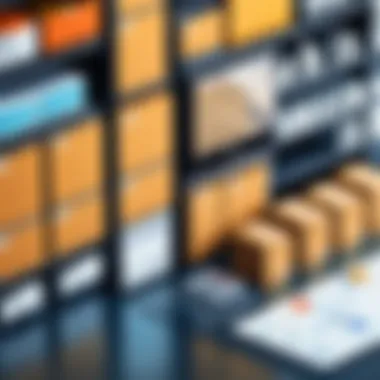
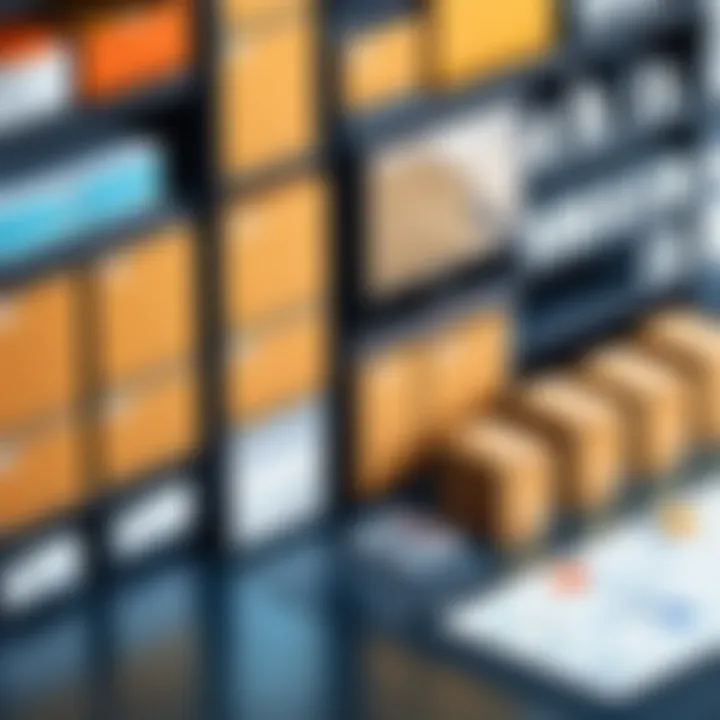
Barcode and RFID technology play a transformative role in inventory management. Barcodes facilitate quick scanning of products, which speeds up the logging process. They reduce the time staff spends on manual entry, thus minimizing inaccuracies. On the other hand, RFID technology provides an even more advanced solution by allowing real-time tracking of items without the need for line-of-sight scanning.
The use of RFID can greatly enhance inventory visibility. Devices read tags on products even from a distance. This helps in maintaining accurate inventory counts and helps identify misplaced items. Businesses that adopt these technologies often see improved accuracy in inventory levels, enhancing overall operational efficiency.
Cloud-Based Solutions
Cloud-based solutions represent another leap forward in inventory management technology. These systems allow users to access inventory data from anywhere, facilitating remote work and decision-making. Additionally, cloud-based inventory management can be easily integrated with other systems, such as accounting software or e-commerce platforms, creating a more seamless flow of information.
Benefits of cloud solutions include scalability. As a business grows, its inventory system can be easily upgraded without substantial investments. This flexibility is particularly valuable for businesses facing fluctuations in demand. Moreover, because data is stored in the cloud, businesses reduce the risk of data loss due to local hardware failures.
"Cloud technology provides businesses with the agility and scalability they need to adapt to changing market conditions."
Data Analytics in Inventory Management
Data analytics plays a pivotal role in inventory management. It enables businesses to optimize their stock levels, reduce waste, and enhance customer satisfaction. By leveraging data analytics, companies can gain insights into their inventory processes, identifying trends and inefficiencies that would otherwise go unnoticed. The evolving nature of business demands a shift from traditional methods to more data-driven approaches. This transition holds significant benefits for organizations that seek to stay competitive in a rapidly changing market.
Role of Forecasting
Forecasting is an essential aspect of inventory management. It refers to the process of predicting future demand for products based on historical data, market trends, and seasonal variations. Accurate forecasting helps businesses plan their inventory more effectively, ensuring they maintain the right amount of stock to meet customer needs without overstocking.
Key benefits of effective forecasting include:
- Reduced carrying costs: By maintaining optimal inventory levels, businesses can minimize the costs associated with storing excess products.
- Enhanced customer satisfaction: When products are available when needed, customer satisfaction increases, leading to repeat business.
- Improved cash flow: Well-managed inventory allows companies to allocate funds more efficiently, as they are not tied up in excess stock.
Real-Time Data Monitoring
Real-time data monitoring allows businesses to have an up-to-date view of their inventory status. This capability is critical in making informed decisions quickly. With real-time monitoring, organizations can track inventory levels, sales patterns, and supply chain intricacies continuously.
The advantages of real-time data monitoring include:
- Immediate insights: Businesses can spot trends or anomalies as they happen, enabling swift responses to fluctuations in demand.
- Reduction in stockouts: By closely monitoring inventory levels, companies can anticipate shortages and reorder before running out.
- Enhanced accuracy: Accurate, immediate data helps in maintaining precise inventory records, reducing the likelihood of errors.
Impact of Big Data
Big data has transformed how inventory management is approached. With vast amounts of data being generated from multiple sources, businesses can now analyze information on a scale previously unimaginable. This analysis leads to more informed decisions and optimized inventory strategies.
The impact of big data includes:
- Predictive analytics: Companies can use big data to identify patterns and forecast future demands.
- Enhanced segmentation: Businesses can categorize inventory more efficiently, focusing on optimizing high-turnover items.
- Supply chain visibility: Big data technologies improve visibility along the entire supply chain, facilitating better planning and responsiveness.
"Leveraging data analytics in inventory management is no longer an option but a necessity for businesses looking to thrive in todayโs competitive landscape."
Best Practices for Inventory Optimization
Effective inventory management is essential in maintaining smooth operational processes. The best practices for inventory optimization provide businesses with methods to enhance both efficiency and effectiveness in their inventory management practices. These methods aim to lower costs, improve accuracy, and increase service levels. Implementing these practices can lead to significant improvements in a company's overall supply chain performance.
Regular Inventory Audits
Regular inventory audits are a critical component of good inventory management. Conducting these audits allows companies to maintain accurate records while reconciling discrepancies between physical counts and reported figures. It helps in identifying slow-moving items and excess stock, which can contribute to overstock and increased holding costs.
- Types of Audits: Organizations can perform various types of audits, including cycle counts, annual physical inventory counts, and spot checks. Each method has its own advantages, and organizations should choose based on their specific needs.
- Benefits: Regular audits lead to better data integrity, reduced risk of stockouts, and enhanced decision-making.
- Considerations: It is essential to schedule audits during less busy periods to minimize disruption and ensure thorough checks. Proper staff training also plays an important role in successful audits.
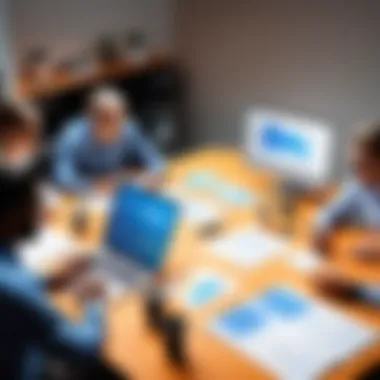
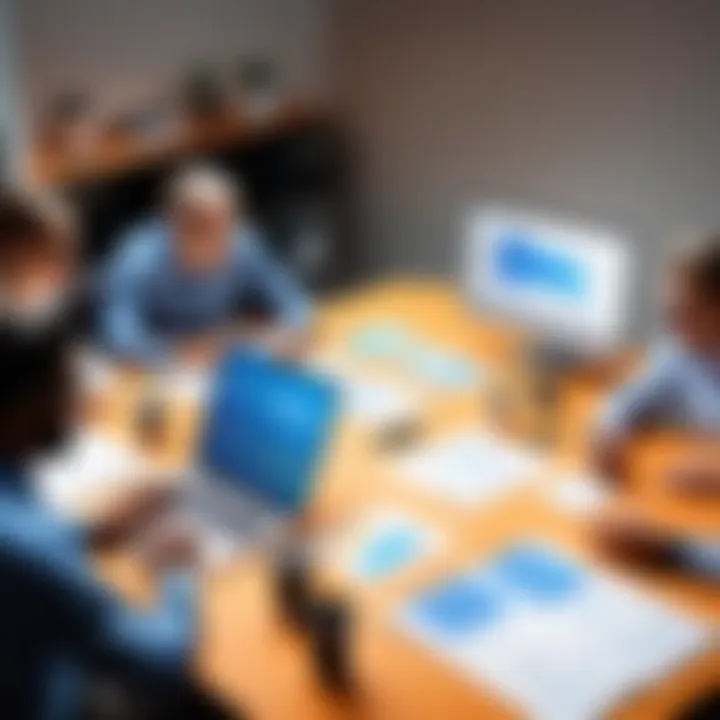
Cross-Functional Collaboration
Cross-functional collaboration is vital for optimizing inventory management. Collaboration among different departmentsโsuch as procurement, sales, IT, and operationsโfacilitates a unified approach towards inventory management.
- Enhanced Communication: Regular updates and information sharing about inventory levels can help prevent stockouts and optimize order cycles.
- Data Sharing: Teams can analyze sales trends and customer demands collectively to maintain appropriate inventory levels. This also helps in identifying misalignment between supply and demand.
- Benefits: By working together, organizations can achieve a holistic view of inventory, improving forecasting accuracy and operational responsiveness.
Establishing Reorder Points
Establishing reorder points is a strategy that improves inventory flow and reduces the risk of stockouts. A reorder point determines the inventory level where a new order should be placed to replenish stock before it runs out.
- Calculation: Reorder points should consider lead time and average usage. For example, if a product has a lead time of two weeks and an average weekly demand of 10 units, the reorder point could be set at 20 units.
- Flexibility: Regularly review these points based on changing sales trends, seasonal fluctuations, or disruptions in supply.
- Benefits: Proper reorder points ensure that inventory is maintained at optimal levels, reducing excess stock and minimizing carrying costs.
Understanding and implementing these practices can drastically influence the overall operational efficiency of inventory management.
By applying these best practices, businesses can optimize their inventory processes, adapt to market changes, and ultimately improve customer satisfaction.
Challenges in Inventory Management
Inventory management is an essential aspect of modern business operations, yet it comes with its share of challenges. Understanding these challenges helps organizations address them effectively and optimize their inventory processes. Each challenge represents a potential risk that can disrupt operations or lead to financial loss. Being aware of these elements is crucial for decision-makers aiming to improve efficiency and reduce waste.
Supply Chain Disruptions
Supply chain disruptions can occur due to various reasons, including natural disasters, supplier failures, or geopolitical events. These interruptions can significantly impact inventory availability. When a supply chain is disrupted, businesses may face delays in receiving raw materials or finished goods, leading to potential stockouts. Handling these disruptions is critical for maintaining a steady flow of goods to customers. Companies often need to adopt contingency plans which include diversifying suppliers and maintaining safety stock levels. This helps reduce the risk of having insufficient inventory during unforeseen events.
Inaccurate Inventory Data
Accuracy in inventory data is paramount for effective management. Inaccurate data can stem from manual entry errors, improper tracking methods, or lack of regular audits. This inaccuracy often leads to poor decision-making regarding stock levels and reorder points. For example, a business may believe it has sufficient stock when it does not, resulting in missed sales opportunities. Conversely, overestimating stock levels can lead to overstock situations, which increase carrying costs. To combat this issue, companies should implement robust data monitoring practices using technology solutions that provide real-time visibility into inventory levels.
Overstock and Stockouts
Overstock and stockouts are two sides of the same coin that can hamper inventory efficiency. Overstock occurs when inventory levels exceed customer demand, resulting in tied-up capital and storage costs. Conversely, stockouts happen when inventory is insufficient to meet demand, leading to lost sales and customer dissatisfaction. Both phenomena can be detrimental to a business's bottom line. Proper forecasting techniques and regular inventory reviews are essential to balance stock levels. By utilizing data analytics and demand forecasting tools, companies can better align inventory with market needs.
Key Takeaway: Addressing challenges in inventory management is crucial for maintaining operational efficiency. Businesses must focus on supply chain resilience, accurate data management, and achieving the right balance between overstock and stockouts. Investing in technology and adopting best practices can lead to significant improvements in inventory performance.
The Future of Inventory Management
The future of inventory management holds significant promise as businesses seek to enhance their strategies through technology and innovative methodologies. Inventory management is evolving rapidly in response to dynamic market conditions and customer expectations. Companies that adapt to these changes can expect improved efficiency, reduced costs, and heightened customer satisfaction.
Key elements driving this evolution include technological advancements, changing consumer behavior, and the need for more adaptive and responsive systems. Businesses must stay ahead of these developments to ensure that their inventory management practices remain effective and competitive.
Emerging Trends
Several emerging trends are reshaping how businesses approach inventory management. Automation is at the forefront, streamlining various processes. Companies increasingly employ robotics and automated systems to manage stock levels, improve accuracy in order fulfillment, and reduce labor costs. Additionally, the integration of the Internet of Things (IoT) offers real-time monitoring of inventory levels, providing valuable insights into stock movement and enabling proactive decision-making.
- Here are some notable trends in inventory management:
- Adoption of blockchain technology for transparent supply chains.
- Emphasis on sustainability and eco-friendly practices.
- A shift towards omnichannel retail strategies, providing a seamless customer experience.
- Increased use of predictive analytics for better forecasting.
These trends indicate a clear movement towards harnessing technology to meet the challenges of inventory management.
Integration of AI and Machine Learning
Artificial Intelligence (AI) and Machine Learning (ML) are becoming integral components of effective inventory management. These technologies enable businesses to analyze vast amounts of data to uncover patterns and trends that inform better decision-making.
AI algorithms can optimize stock levels by predicting demand more accurately based on various factors, such as seasonality and market trends. This predictive capability minimizes instances of overstock and stockouts, leading to enhanced operational efficiency. Machine Learning also aids in anomaly detection, identifying discrepancies in inventory data that may suggest errors or fraud.
Using AI can lead to several benefits:
- Increased accuracy in inventory tracking.
- Enhanced responsiveness to market changes.
- Improved customer satisfaction through timely fulfillment.