ERP Solutions for Small Manufacturers
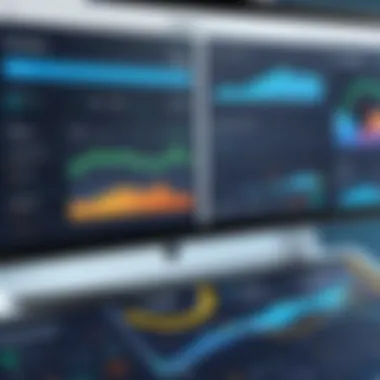
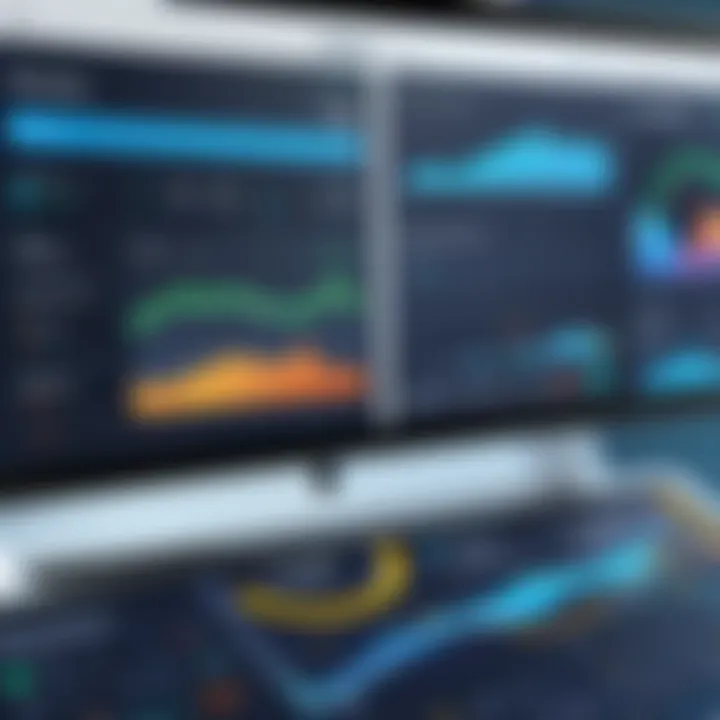
Intro
The small manufacturing sector plays a crucial role in the economy. These businesses often face unique challenges that can sometimes stifle growth and efficiency. One way to combat these obstacles is through the implementation of Enterprise Resource Planning (ERP) systems. This article explores the myriad benefits of ERP solutions tailored specifically for small manufacturers. By examining key features, pricing models, and practical strategies, this guide aims to provide decision-makers with a well-rounded understanding of how ERP systems can enhance productivity and streamline operations.
Key Features
Overview of Features
ERP systems bring several core features that are essential for small manufacturers. These include:
- Inventory Management: An efficient ERP can track stock levels in real-time, reducing the chances of overstocking or stockouts.
- Production Planning: Proper scheduling is critical for meeting customer demands while managing resources efficiently.
- Financial Management: ERP systems help automate financial processes, providing a comprehensive view of budget and performance.
- Reporting and Analytics: Reporting tools allow businesses to analyze data trends, making informed decisions on production and sales.
- Customer Relationship Management (CRM): Integrating CRM features helps maintain strong customer relationships and customer data management.
Unique Selling Propositions
Each ERP solution has its strengths, which can be vital for small manufacturers. Some unique selling propositions to consider include:
- Customization: Many ERP systems offer customization options that can be tailored to the specific needs of a small manufacturing operation.
- Scalability: As businesses grow, their requirements change. Scalable solutions ensure that manufacturers can adapt without requiring a complete overhaul of their system.
- User-Friendliness: Small manufacturers may not have extensive IT resources. Therefore, a user-friendly interface can simplify implementation and reduce training costs.
Pricing Models
Different Pricing Tiers
Understanding the cost structure of ERP solutions is essential. Most ERP systems offer various pricing tiers based on:
- Functionality: Basic features at lower tiers to advanced functionalities at higher tiers.
- User Licenses: Costs can vary with the number of users, which is significant for small teams.
- Deployment Options: On-premises solutions tend to have high initial costs, while cloud solutions usually have subscription-based models.
ROI and Cost-Benefit Analysis
Before implementing an ERP system, businesses should conduct a cost-benefit analysis to gauge potential returns on investment. Factors to consider include:
- Operational Efficiency: Reductions in manual processes can lead to faster turnaround times and lower operational costs.
- Error Reduction: Minimizing human error saves money and resources in the long run.
- Increased Sales: Better inventory and production management often result in improved sales metrics.
"The insightful integration of ERP systems can transform the operational landscape for small manufacturers, fostering growth and enhancing sustainability."
Investing in an ERP system is not just about software; it's about future-proofing small manufacturing businesses against evolving market demands. In the sections that follow, we will analyze implementation strategies and further explore the advantages of adopting ERP software.
Prologue to ERP Systems
Enterprise Resource Planning (ERP) systems play a crucial role in modern manufacturing environments, especially for small manufacturers who are often juggling multiple tasks with limited resources. Understanding what ERP systems are and their significance is essential for businesses aiming to streamline their operations. ERP solutions integrate various functions into one complete system to streamline processes and information across the organization. This integration can lead to improved efficiency and productivity, positioning small manufacturers favorably in a competitive landscape.
Definition of ERP
ERP stands for Enterprise Resource Planning. It is a type of software used by organizations to manage day-to-day activities. ERP software integrates core business processes, including procurement, manufacturing, service delivery, project management, financials, and inventory control. The main goal of ERP is to provide a comprehensive view of business operations and help organizations make informed decisions.
In essence, ERP serves as a centralized hub for data, connecting different departments and promoting collaboration. Small manufacturers often benefit from this type of system, as it allows them to manage diverse processes within a unified platform.
Importance of ERP in Manufacturing
ERP systems are significantly important in the manufacturing sector for several reasons. Firstly, they enhance operational efficiency by automating routine tasks. This reduces the likelihood of errors and frees up time for staff to focus on strategic activities. Secondly, ERP systems enable better inventory management. Small manufacturers can track inventory levels in real time, leading to improved stock control and minimized wastage.
Moreover, an ERP system can provide valuable insights through data analysis. Businesses can analyze production trends and financial performance, allowing for data-driven decision-making.
Another critical aspect is the scalability of ERP solutions. As small manufacturers grow, the need for scalable systems becomes apparent. ERP systems can adapt to changing requirements and increased volumes of transactions, thus supporting business growth.
"Adopting an ERP system is not just about technology; it is about reshaping organizational processes to achieve greater efficiency."
Unique Challenges for Small Manufacturers
Small manufacturers face a variety of unique challenges that can impact their operations significantly. Understanding these challenges is vital for making informed decisions about adopting ERP systems. These systems can provide the tools needed to address specific obstacles but knowing what these obstacles are is the first step in the decision-making process.
Resource Limitations
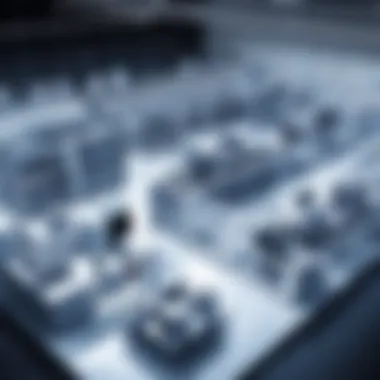
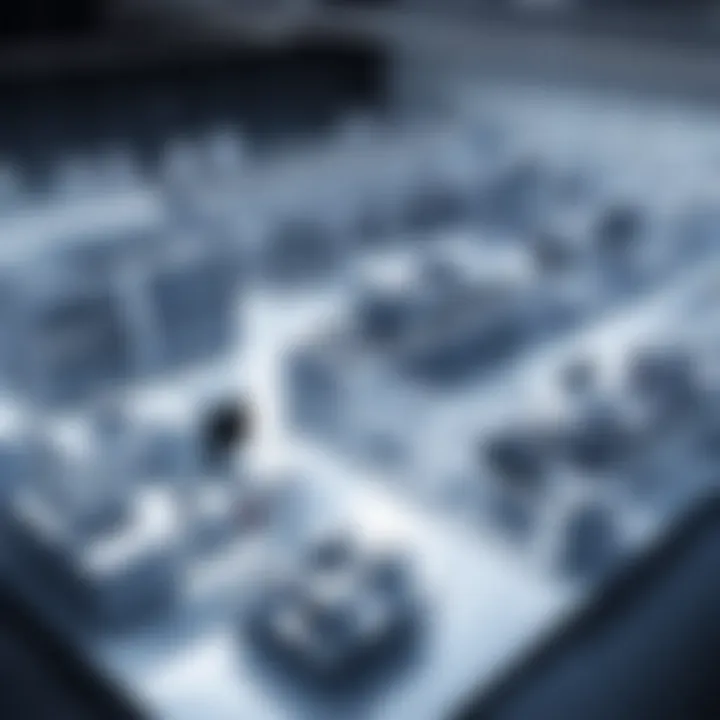
One of the foremost challenges small manufacturers encounter is limited resources. These limitations can manifest in various forms, such as a constrained budget, inadequate staff, or insufficient technology infrastructure. Unlike larger corporations, small manufacturers often operate with tighter financial margins, making it crucial to optimize every aspect of their business.
As a result, investing in technology can be daunting. The upfront cost of an ERP system may seem hefty compared to the relatively gradual return on investment. Many small manufacturers struggle to allocate funds toward an ERP implementation, fearing it may divert resources from other essential areas.
However, it is important to recognize that an ERP system can streamline operations, ultimately leading to cost savings and efficiency improvements. By integrating various functions such as inventory management and production planning into a single platform, manufacturers can eliminate redundancies, improve accuracy, and respond faster to market demands.
Complexity of Operations
Another significant challenge that small manufacturers face is the complexity of their operations. Manufacturing processes can involve numerous steps, from procurement to production to distribution. Managing these processes can be particularly challenging without a centralized system to maintain oversight.
Small manufacturers often juggle multiple suppliers, handle varying production cycles, and adhere to fluctuating regulations. This complexity can lead to operational inefficiencies and make it difficult for decision-makers to have a complete view of their business.
An ERP system can mitigate these challenges by providing a cohesive interface for managing processes. With such a system in place, small manufacturers can track orders, manage inventories in real-time, and ensure compliance with industry standards.
Key Features of ERP for Small Manufacturers
The effective implementation of an ERP system can be transformative for small manufacturers. It is vital to understand key features that directly address the unique challenges faced by these businesses. Each feature contributes not only to operational efficiency but also to informed decision-making. Thus, selecting an ERP solution tailored for small manufacturers is crucial.
Inventory Management
Inventory management is a core component of ERP systems for small manufacturers. It enables real-time tracking of inventory levels, orders, and deliveries. This functionality allows businesses to maintain optimal stock levels, minimizing both surplus and shortages. The system can predict inventory needs based on historical data and trends, reducing carrying costs.
Furthermore, automated inventory management reduces human error. This accuracy in inventory data is critical. It empowers managers to make data-driven decisions regarding purchasing and stock control. Ultimately, better inventory management leads to improved customer satisfaction through timely deliveries and reduced lead times.
Production Planning
Production planning is essential for optimizing workflow and resource allocation within a manufacturing environment. ERP systems facilitate comprehensive planning by offering tools for demand forecasting and production scheduling. With accurate demand forecasting, small manufacturers can align production schedules accordingly. This foresight can mitigate waste and ensure that production capacity meets customer demands efficiently.
The production planning module often integrates seamlessly with other system features. When combined with inventory management, it provides a holistic view of available resources, enabling just-in-time production practices. This integration supports better responsiveness in a competitive market, allowing manufacturers to adjust quickly to changes in demand or resource availability.
Financial Management
Financial management is another critical feature of ERP solutions for small manufacturers. An integrated financial management module streamlines accounting tasks, such as budgeting, invoicing, and financial reporting. This integration ensures that financial data is synchronized across all departments, enhancing visibility and accuracy.
Moreover, effective financial management allows small manufacturers to analyze costs, identify profitable products, and generate tailored financial reports for stakeholders. By having real-time financial insights, manufacturers can make strategic decisions regarding investments and resource allocation. This clarity is essential for sustainable growth and navigating economic changes.
In summary, the key features of ERP systems for small manufacturers—inventory management, production planning, and financial management—are integral. They enable small manufacturers to enhance efficiency, optimize resources, and make informed decisions. As such, understanding these features is a critical step in selecting the right ERP system.
Selecting the Right ERP System
Selecting the right Enterprise Resource Planning (ERP) system is crucial for small manufacturers. It encapsulates not just the technology deployment, but the broader strategy that influences operational efficiency. Opting for the right system can lead to significant gains in productivity and streamline processes.
Evaluating Business Needs
Understanding specific business needs is the first step in the selection process. Small manufacturers often operate in unique environments, with distinct processes and constrained resources. Thus, a one-size-fits-all approach will not yield optimal results.
- Identify Core Functions: It is important to pinpoint what functions are most critical. Is inventory management crucial, or does your company need robust production planning? Assessing priorities enables the selection of an ERP system that fits well with operational needs.
- Gather Input from Stakeholders: Involve team members from various departments in the evaluation. Their insights can illuminate specific challenges and requirements that may not be apparent to decision-makers alone.
- Future Projections: Consider where the business will be in a few years. Ensure that the selected ERP system can grow with the company. This foresight is essential; otherwise, the investment may become obsolete too quickly.
Taking the time to thoroughly evaluate these elements forms the foundation for a successful ERP implementation.
Scalability Considerations
Scalability is another essential aspect when selecting an ERP system. As small manufacturers grow or adapt to market changes, the system must be able to accommodate this evolution.
- Flexible Architecture: Look for ERP systems that have a modular structure. This allows for the addition or removal of components as necessary, aligning the software capability with business needs over time.
- Cost-Effectiveness: Ensure that adding new functionalities to the ERP system doesn’t come at an exorbitant cost. Assess pricing models and any potential increase in subscription fees when scaling.
- Vendor Support: Investigate the vendor's reputation for supporting system upgrades and expansions. Reliable support can ease the transition as the business scales.
Negotiating these factors can avoid the pitfall of investing in a solution that becomes a burden instead of an enabler.
Implementation Strategies
Implementation of an ERP system is not just a technological change; it is a transformational process that requires careful planning and execution. For small manufacturers, the importance of choosing the right implementation strategy cannot be underestimated. A well-thought-out approach can lead to smoother transitions, reduced risk of failure, and more significant gains in operational efficiency. The primary objective in this phase is to align the deployment of the ERP system with the unique needs of the organization while minimizing disruption to daily operations.
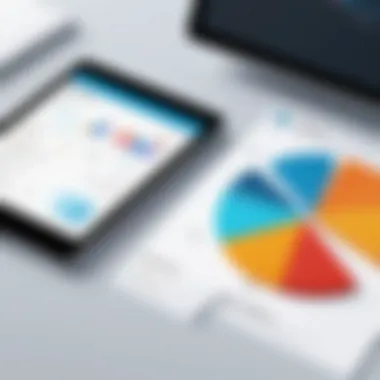
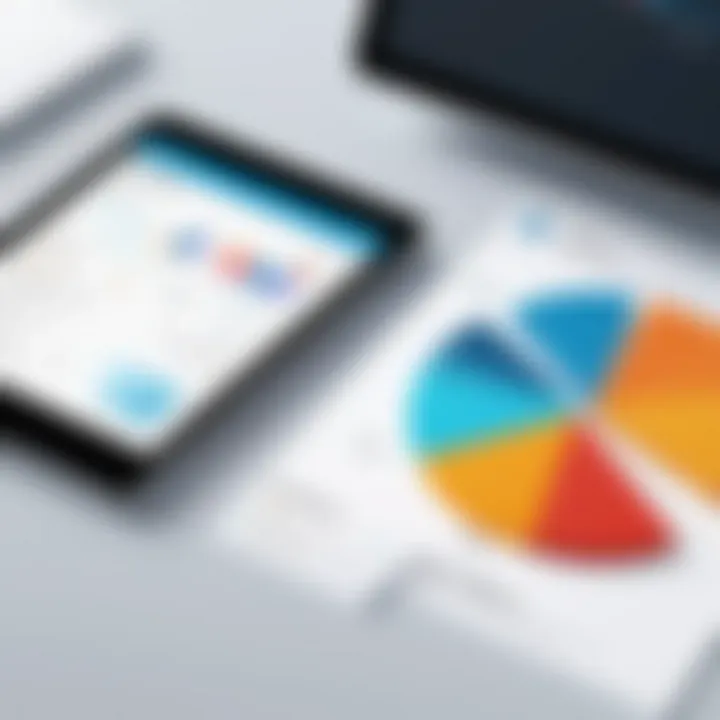
The two commonly adopted strategies for implementation are phased implementation and big bang implementation. Each approach presents its own merits and challenges, and the choice between them largely depends on the specific situation of the manufacturer, available resources, and readiness of staff. It is essential for decision-makers to consider how these implementation strategies impact not only the technology adoption but also the company culture and employee engagement.
Phased Implementation
Phased implementation is a gradual approach that involves rolling out the ERP system in manageable parts. This allows the organization to introduce new processes incrementally, which can alleviate the overwhelm that often accompanies significant change. Small manufacturers particularly benefit from this method. It reduces risks and offers a chance to adjust the system based on feedback before the full implementation.
Benefits of Phased Implementation:
- Reduced Risk: By implementing in stages, manufacturers can identify and mitigate issues as they arise before system-wide deployment.
- Continuous Improvement: Each phase serves as a learning opportunity. Feedback can be gathered and used to improve subsequent phases.
- Less Disruption: Employees can adapt gradually. This is crucial in small manufacturing firms where even a small disruption can affect production.
Considerations for Phased Implementation:
- Longer Timeline: While risks may decrease, the total time to complete the implementation may extend.
- Coordination Challenges: Each phase requires careful planning to ensure that all components interact correctly.
Training of Staff
An often underestimated component of ERP implementation is staff training. The success of an ERP system is closely tied to how well users understand and utilize the tools provided. For small manufacturers, where employee roles may stretch across various responsibilities, investement in training is essential. Training ensures that users feel competent and confident in using the new system, which translates to productivity gains.
Effective Training Strategies:
- Tailored Training Programs: Focus on the specific needs of different user groups. Frontline employees may need different training than those in a managerial role.
- Hands-On Workshops: Practical, interactive sessions engage users and allow them to learn the system in a real-world setting.
- Ongoing Support: Post-implementation support helps users resolve issues and continuously improve their skills as they adapt to the new system.
Effective staff training leads to increased adoption rates of the ERP system, resulting in greater potential for efficiency and accuracy within the organization.
Cost Considerations for Small Manufacturers
Understanding the cost considerations for small manufacturers who are contemplating an ERP solution is critical for successful implementation and long-term sustainability. The investment in ERP systems can be significant. However, the potential benefits, including improved efficiency and productivity, can outweigh these costs. This section will discuss the two primary cost elements: initial investment and ongoing maintenance costs.
Initial Investment
The initial investment in an ERP system includes several components. First, purchase prices of the software can vary widely. Some solutions are cloud-based with subscription models, while others demand a one-time licensing fee. Cloud-based platforms such as NetSuite or SAP Business ByDesign may have lower upfront costs compared to on-premise solutions but still entail consistent payments over time, which can accumulate.
Another important aspect is hardware requirements. If the ERP solution is on-premises, additional investment in servers and networking equipment may be required. This often includes ensuring that existing infrastructure can support the new system. In some cases, small manufacturers decide to upgrade their current systems or replace outdated hardware to meet system requirements.
Furthermore, implementation services contribute to the initial investment. Many vendors offer assistance in deploying the software, which can include consultation, system configuration, data migration, and user training. The costs of hiring experienced consultants or in-house IT personnel can quickly add up. To effectively manage these expenses, small manufacturers need to negotiate clear contracts and scope of work with vendors.
A proper budgeting strategy must account for these various elements, ensuring that unforeseen costs do not derail the project. In summary, considering the specific needs of their operation, manufacturers must carefully evaluate and understand the total initial investment before committing.
Ongoing Maintenance Costs
Ongoing maintenance costs are the next crucial aspect of ERP financial planning. Once the system is in place, small manufacturers must consider costs for software updates, technical support, and training for new staff. Most ERP vendors, including Microsoft Dynamics 365 and Oracle ERP Cloud, charge annual fees for customer support and software updates, which is usually a percentage of the initial license fee.
Additionally, infrastructure maintenance should not be overlooked. For on-premises solutions, the company must ensure systems are continuously updated and secure, necessitating IT resources or external IT support. This can lead to additional, unplanned financial obligations.
Training is also a significant ongoing cost. As new employees come on board, they will require training on the ERP system, which might involve extra expenses. A competent team can help reduce errors and improve efficiency, but the need for constant learning creates a recurring cost.
Ongoing costs can absorb an organization’s financial resources. Proper planning and assessment of the system's value are essential to maintain a balanced budget.
Comparative Analysis: ERP vs. Other Software Solutions
Understanding the different software solutions available is pivotal for small manufacturers. An ERP system is not the only option but it stands out for its integrated approach to business management. In this section, we focus on comparing ERP systems with standalone applications and custom software solutions. Each has its own merits and limitations, making it essential to evaluate them based on specific operational needs.
ERP vs. Standalone Applications
Standalone applications are designed to handle particular tasks such as accounting, inventory, or customer relationship management. While these applications excel in their specific functions, they can create silos of information. Data may not flow seamlessly between them, leading to inefficiencies and potential errors in information management.
Key Considerations:
- Integration: ERP systems offer a central repository of information, integrating all facets of operations, which is a significant advantage over standalone applications.
- Increased Efficiency: By consolidating various functions into one system, ERP reduces time spent on data entry and retrieval. This can result in faster decision-making.
- Scalability: As a small manufacturer grows, an ERP adapts easily to changing needs, unlike standalone systems that often require replacement.
"Choosing an ERP system over standalone applications allows small manufacturers to streamline their processes and minimize operational silos."
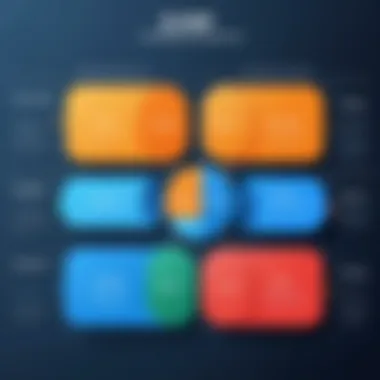
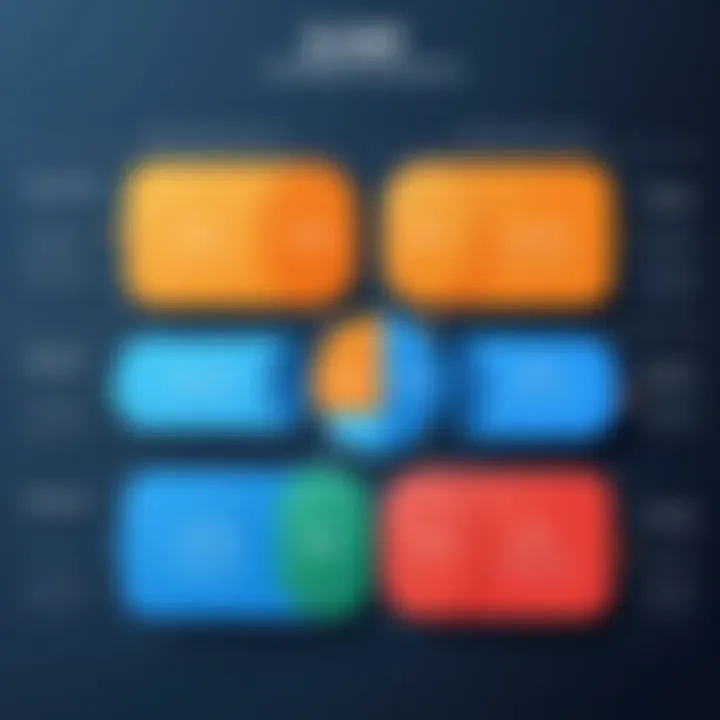
In summary, while standalone applications serve specific functions well, they often lack the comprehensive capabilities required by small manufacturers to enhance overall efficiency.
ERP vs. Custom Software Solutions
Custom software solutions are built to meet the unique needs of a business. They offer flexibility but come with their own set of challenges. While custom solutions may seem appealing due to their tailored nature, they often require more resources for development and maintenance compared to standard ERP systems.
Key Considerations:
- Time-Consuming Development: Custom solutions can take significant time to develop. In contrast, ERP systems are usually available for quicker implementation.
- Higher Maintenance Costs: Custom software often incurs continuous costs for updates and support. ERP typically includes ongoing support services as part of its package.
- Limited Features: Custom solutions might exclude features available in ERP systems, which can be crucial for small manufacturers looking to optimize their processes.
In essence, while custom software offers personalization, the trade-offs in cost, time, and resource allocation often favor the implementation of an ERP solution for small manufacturers striving for operational excellence.
Success Stories: Case Studies of ERP Implementation
The exploration of success stories and case studies of ERP implementation is vital for small manufacturers looking to adopt these systems. By reviewing real-world examples, businesses can gain valuable insights into the practical applicability of ERP solutions. They can see how others in similar situations have navigated challenges and reaped rewards from their ERP investments. Case studies function as proof-of-concept materials, demonstrating not just theoretical advantages but tangible outcomes.
Moreover, these stories illustrate various approaches to implementation. They highlight the diversity in manufacturing operations, showing that one size does not fit all. Each case offers unique takeaways regarding the specific challenges faced during the implementation process and how these challenges were overcome. This presents an opportunity for potential users to benchmark their expectations and strategies.
Case Study Overview
Examining case studies allows potential ERP users to learn from the experiences of those who have successfully adopted systems tailored to small manufacturing. For instance, consider the case of a small electronics manufacturer called TechGadgets. Before ERP implementation, TechGadgets struggled with inventory management and order fulfillment. Orders were frequently delayed, leading to customer dissatisfaction. With careful evaluation, they implemented SAP Business One. This decision was driven by the need for an integrated solution that provided visibility across all areas of their operations. The implementation process took six months and involved customized training and phased rollout to minimize disruption. By contrasting TechGadgets’ challenges with their outcomes, we can assess how effective the ERP system was in addressing specific pain points.
Outcomes and Benefits
The results of TechGadgets' ERP adoption were profound. Key outcomes included:
- Enhanced Inventory Accuracy: The company reported a 30% reduction in excess inventory. They were able to synchronize supply with demand, leading to better cash flow.
- Improved Order Fulfillment: Order processing times decreased by 40%. Customers received their products faster, which dramatically improved satisfaction ratings.
- Increased Operational Efficiency: By automating repetitive tasks, employees could focus on more strategic initiatives, such as product development or customer engagement. This led to a 25% increase in productivity.
- Revenue Growth: Post-implementation, TechGadgets saw revenue increase by 15%, primarily from higher customer retention rates and improved market share.
These results underscore the importance of aligning ERP systems with unique business objectives. This case clearly illustrates how effective ERP implementation can lead not only to immediate operational improvements but also to long-term gains in market position.
"Learning from successful implementations allows us to prioritize key areas for improvement. Every story offers lessons that others can apply to their contexts."
This understanding highlights not just the necessity but the potential ROI of an ERP system for small manufacturers. Each success story serves as a guiding narrative that can inspire and inform decision-making for companies considering an ERP system.
Future Trends in ERP for Small Manufacturers
The landscape of ERP (Enterprise Resource Planning) continues to evolve, especially for small manufacturers. Understanding the future trends in ERP solutions is crucial for these companies as they seek to leverage technology for better efficiency and competitiveness. Embracing modern trends not only helps in adapting to market changes but also in streamlining operations. Small manufacturers that remain informed about advancements will be better situated to make strategic decisions regarding technology adoption.
Cloud-Based ERP Solutions
Cloud-based ERP solutions are becoming increasingly essential for small manufacturers. The shift to the cloud is driven by several factors, including flexibility, scalability, and cost-effectiveness. Small manufacturers often face limitations in their IT capabilities and resources. Cloud ERP helps alleviate these concerns by offering a subscription-based model that reduces upfront costs. This enables smaller firms to access features typically reserved for larger organizations without heavy investment.
Additionally, cloud solutions provide real-time data access. This allows decision-makers to access critical information anywhere and at any time. Another advantage is the automatic updates that cloud providers offer, ensuring that manufacturers are always using the most up-to-date software.
Furthermore, cloud ERP offers enhanced collaboration. Teams can work together seamlessly, regardless of location. This aligns well with the modern trend of remote work. Companies can also integrate with other cloud applications, creating a more cohesive operational workflow.
Integration with IoT
Integration with the Internet of Things (IoT) is another significant trend influencing ERP solutions for small manufacturers. IoT devices can collect valuable data from machinery and production lines. By integrating this data into an ERP system, small manufacturers can gain insights into production efficiency, equipment performance, and supply chain management.
Using IoT data allows for predictive maintenance, reducing downtime and minimizing costs associated with unplanned repairs. It also facilitates better inventory management by providing real-time data on stock levels and product movement.
Moreover, IoT integration supports data-driven decision-making. Manufacturers can analyze trends and patterns, leading to improved operational strategies and resource allocation. In essence, small manufacturers that adopt IoT integrations into their ERP systems position themselves to not only react to challenges but also proactively improve processes.
"Embracing cloud technology and IoT integration places small manufacturers at the forefront of innovation, enabling them to optimize operations and achieve greater competitiveness."
Overall, staying aware of these trends—cloud-based solutions and IoT integration—can guide small manufacturers in making informed decisions about their ERP strategies. By focusing on these future developments, they are more likely to achieve success in an increasingly competitive market.
Culmination
The conclusion of this article brings together the essential themes surrounding ERP systems for small manufacturers. It is vital to understand how these solutions can directly address specific industry challenges. Notably, ERP systems enhance operational efficiency and overall productivity by unifying various business functions into a single cohesive platform.
Summary of Key Points
In summary, we have examined several crucial aspects:
- Importance of ERP: The article illustrated how ERP systems streamline business processes, especially in small manufacturing environments.
- Challenges Faced: Small manufacturers often grapple with resource limitations and complex operational needs, both of which ERP can mitigate.
- Key Features: We discussed how features like inventory management, production planning, and financial management cater uniquely to the requirements of small manufacturers.
- Implementation Strategies: Successful ERP deployment hinges on strategic implementation plans and staff training, ensuring the system is utilized to its fullest potential.
- Cost Considerations: We have analyzed initial investment versus ongoing costs, helping businesses make informed financial decisions.
- Comparative Analysis: The discussion around ERP versus other software solutions has highlighted the comprehensive advantages ERP brings in operational contexts.
- Future Trends: Cloud-based solutions and IoT integration will reshape ERP functionalities, making them more accessible and impactful for small manufacturers in the coming years.
"Implementing an ERP system is not merely a technological upgrade; it is a transformation in how business operates."