Top Design Software Choices for Mechanical Engineers
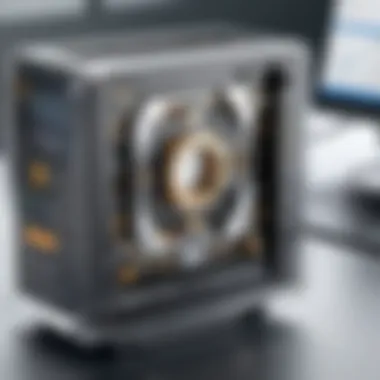
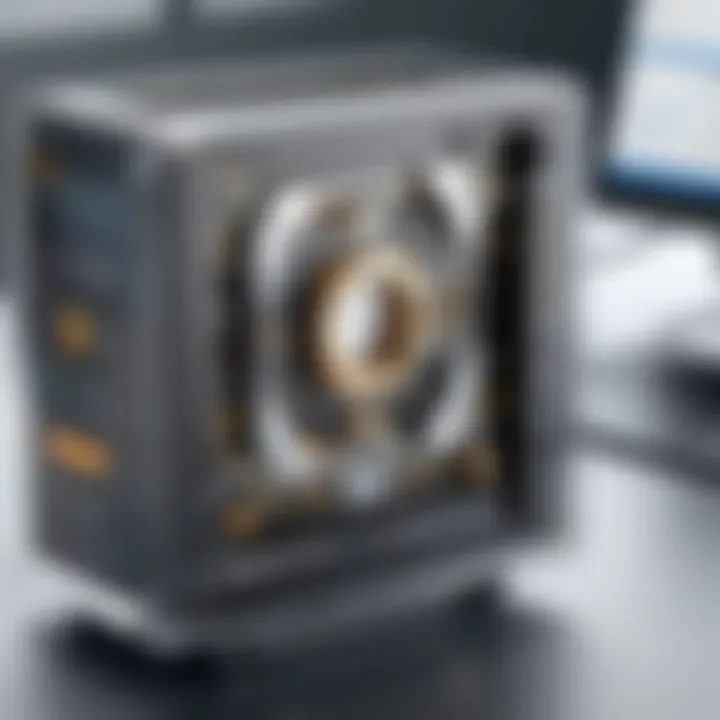
Intro
The realm of mechanical engineering is littered with complex challenges that require precise solutions. As engineers strive to design robust products, they also need tools that simplify collaboration and enhance creativity. This is where design software comes into play. With ever-evolving technology, selecting the right design software can feel akin to finding a needle in a haystack. However, honing in on essential software designed specifically for mechanical engineers makes the task more manageable.
The tools available today range from traditional CAD applications to innovative simulations and advanced visualization programs. Each software package boasted unique characteristics tailored to meet specific needs, yet all aim to streamline workflows and optimize design processes. The challenge lies in navigating the multitude of options to find solutions that not only fit individual projects, but also align with overarching organizational goals. Understanding the key features, advantages, and pricing models of various design software can lead to better decision-making and improved efficiency in engineering practices.
In the sections that follow, we will delve into the primary features of essential design software and discuss aspects like pricing models, ensuring we cater to both the seasoned engineers and newcomers alike. By synthesizing this information, we hope to empower mechanical engineers with knowledge that enhances their professional journey.
Understanding the Role of Design Software in Mechanical Engineering
In today's fast-paced world, mechanical engineers face an array of challenges that necessitate efficient and precise solutions. The role of design software has become increasingly crucial in navigating these complexities. Design software serves as the backbone for mechanical engineers, facilitating tasks from conceptualization to production. By utilizing such tools, engineers can streamline processes, validate their designs, and collaborate effectively with teams across various stages of a project.
Definition of Design Software in Mechanical Engineering
Design software refers to specialized applications that assist mechanical engineers in creating, simulating, and analyzing product designs. These tools encompass a wide range of functionalities, enabling professionals to visualize their ideas, perform complex calculations, and generate documentation for manufacturing processes. In mechanical engineering, this software often includes capabilities for Computer-Aided Design (CAD), 3D modeling, and various simulation tools that test the feasibility and performance of designs before they are physically produced.
For instance, SolidWorks and AutoCAD are popular choices that enable engineers to produce intricate models and assemblies in a virtual environment. By moving beyond traditional methods, design software allows for greater iteration and flexibility in the design process, effectively elevating an engineer's ability to innovate.
Importance of Software Selection
Choosing the right design software is a decision that can profoundly impact the success of engineering projects. A poor choice might limit one's ability to meet deadlines, hinder productivity, or lead to costly errors down the line. Therefore, understanding the specific needs of a project and selecting software that aligns with those requirements is essential.
When assessing software options, factors to consider include:
- Scalability: Does the software accommodate future project needs or team expansions?
- User interface: Is the software intuitive enough to minimize the learning curve for team members?
- Integration capabilities: Can it easily connect with other applications and tools you use?
- Support and training resources: Does the provider offer robust support and training materials?
"Investing in the right tools can be as critical as the design itself; without them, engineers could find themselves swimming upstream, against the tide of progress."
In summary, understanding the intricacies of design software in mechanical engineering and the implications of software selection plays a vital role in a project's trajectory. With the right tools, engineers not only enhance their productivity and collaboration but also unlock new avenues for innovation.
Key Features of Effective Design Software
When it comes to mechanical engineering, choosing the right design software isn't just a task, it's a strategic move. The selection process hinges on understanding key features that can significantly impact the quality and efficiency of the design work. Without a firm grasp of these elements, engineers might end up with tools that don't truly meet their unique needs.
CAD Capabilities
Computer-Aided Design (CAD) is at the heart of almost every mechanical project. This isn't just about creating two-dimensional representations; effective CAD capabilities must offer three-dimensional modeling, parametric design, and extensive libraries of standardized components.
Having a robust CAD system means that engineers can create complex geometries and assemblies efficiently. For instance, tools that support parametric design allow for easy modifications that automatically adjust related elements. This saves time and reduces the chance of errors. Moreover, drafting features equipped with smart dimensions can vastly improve the precision of technical drawings, a critical aspect when it comes to manufacturing.
In practice, solid modeling forms the foundation for prototypes, and it's imperative that the software can also handle data management. Users often appreciate applications that integrate with various file formats, ensuring collaboration isnโt hindered by compatibility issues.
Simulation and Analysis Tools
Beyond the initial design phase, simulation and analysis tools play a pivotal role in predicting performance. It's no longer enough to just design; engineers must now simulate real-world conditions to foresee how products will perform. This involves understanding stress analysis, thermal dynamics, and fluid dynamics.
Software with integrated simulation capabilities allows engineers to test and iterate without waiting for physical prototypes. The ability to perform Finite Element Analysis (FEA) or Computational Fluid Dynamics (CFD) means engineers can validate their designs against potential failures before manufacturing.
For instance, if a mechanical part will undergo significant stress during operation, utilizing a software tool that performs stress testing can help identify weak points. This proactive approach doesn't just enhance design reliability, but also significantly lowers production costs by minimizing the risk of design flaws.
"Effective simulation tools can turn guesswork into informed decisions."
Collaboration Functions
In today's interconnected world, collaboration can't be an afterthought; it's a necessity. Mechanical engineering projects often involve multidisciplinary teams spanning various locations. Thus, design software should ideally incorporate features that promote real-time collaboration.
This can encompass cloud storage solutions, allowing team members to work on projects simultaneously, as well as version control to track changes systematically. The facility to leave comments directly on the designs can streamline communication, making project management not only more efficient but also more transparent.
Software that offers easy access via different devices ensures that team members can stay connected, whether they're at the office, on-site, or working remotely. The significance of seamless collaboration is clearโwhen teams can synchronize their efforts and truly hash out ideas, the outcome is invariably a more refined product.
These key features are not just technical specs; they represent a cohesive workflow that can elevate the design process. By selecting software that encompasses potent CAD capabilities, robust simulation tools, and dynamic collaboration functions, mechanical engineers position themselves for success in an increasingly competitive field.
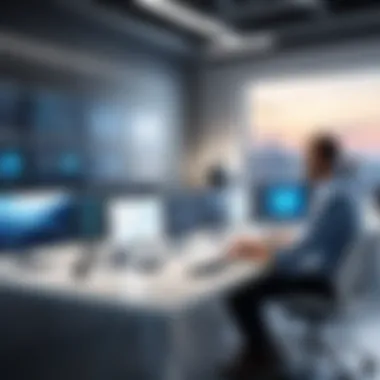
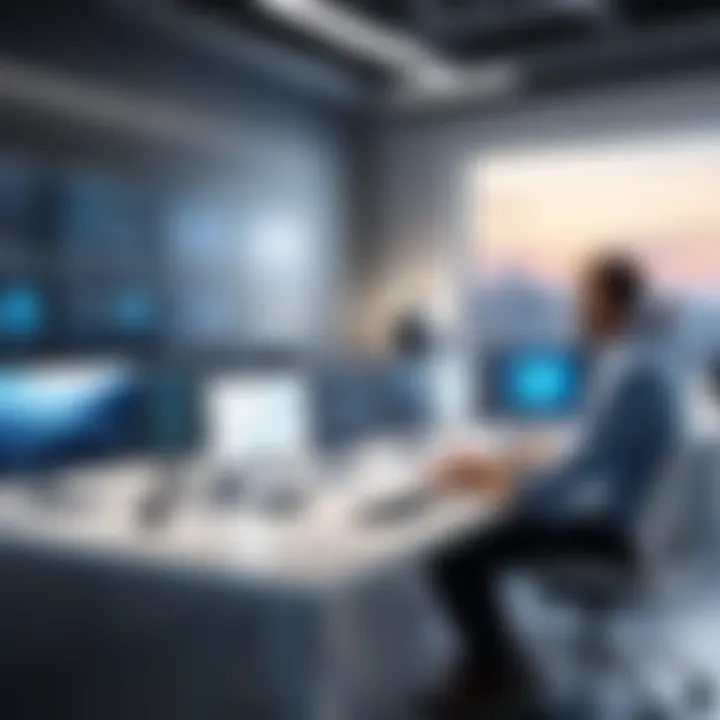
Leading Design Software for Mechanical Engineers
In the rapidly-advancing realm of mechanical engineering, design software serves as the backbone of innovation and productivity. Engineers today are faced with a myriad of tasks that require precision, creativity, and collaboration. Choosing the right software tools can make all the difference in meeting project deadlines and achieving design excellence.
The significance of leading design software lies in its ability to streamline workflows, enhance creative capabilities, and foster communication among team members. It equips engineers with advanced features to simulate, visualize, and implement ideas seamlessly. With an increasing focus on integrated environments, the software landscape now offers solutions that not only cover traditional design phases but also encompass simulation and customer feedback.
With that in mind, let us dig deeper into the specifics of essential design software tools, exploring their features, advantages, and their unique fit for diverse projects.
SolidWorks: A Comprehensive Overview
SolidWorks has emerged as a stalwart in mechanical design software, primarily renowned for its intuitive interface and powerful capabilities. It offers a solid foundation for engineers to create 3D models and assemblies, significantly speeding up the design process.
One of its most impressive features is the ease with which it provides parametric modeling. Engineers can manipulate models instantly by adjusting parameters like dimensions and constraints. It enables quick iterations, allowing for design alterations without starting from scratch. Additionally, SolidWorks integrates well with simulation tools, enabling engineers to test designs under various conditions.
In essence, SolidWorks balances functionality with usability.
AutoCAD Mechanical: Key Features and Benefits
AutoCAD Mechanical stands out with its specialized toolset tailored for mechanical engineering. Its features cater to reducing repetitive tasksโsuch as inserting standard components and creating annotationsโby automating workflows.
This software supports detailed 2D drafting, aligning with industry standards, which is significant in creating precision schematics. It also includes libraries of standard parts and tools, making it highly efficient when designing intricate machines or systems. Beyond the drawing capabilities, it integrates seamlessly with other AutoCAD tools.
Overall, AutoCAD Mechanical is ideal for firms that prioritize accuracy and speed in the design stages.
CATIA: Tailored for Complex Projects
When it comes to handling complex and large-scale projects, CATIA shines as an industry leader. Developed by Dassault Systรจmes, it provides a robust platform for system engineering, from design to manufacturing.
CATIA stands out in aerospace and automotive industries where handling intricate designs and assemblies is a daily affair. Its advanced surface modeling capabilities allow for the creation of smooth, complex shapes that other software might struggle with. Additionally, CATIA is noted for its strong collaboration tools, enabling teams to work on a single project from different geographical locations without losing track of changes.
In summary, CATIA is tailored for high-stakes environments that demand precision and collaboration.
PTC Creo: Flexibility and Customization
PTC Creo is particularly noteworthy for its flexibility and adaptability in design processes. It offers a suite of applications that allow engineers to choose tools they need for specific tasks. This modular approach means teams can equip themselves according to the demands of their projects without being locked into a single workflow.
One of its remarkable features is the ability to create both parametric and direct models within the same environment. This provides a substantial edge when dealing with rapid prototyping and concept development. Furthermore, PTC Creo's extensive visualization tools enhance the presentation of designs, making it easier to convey ideas to stakeholders.
Flexibility is the hallmark of PTC Creo.
Siemens NX: Integrated Solution for Product Design
Siemens NX is an integrated solution that emphasizes the entire product lifecycleโfrom design to manufacturing. Its advanced capabilities combine mechanical design, simulation, and manufacturing in one platform, creating a holistic environment for engineers.
One key aspect of Siemens NX is its focus on generative design. Engineers can explore a wide range of design alternatives based on performance requirements, pushing boundaries in innovation. The software's robust simulation features allow for real-time testing, crucial for validating designs before they move to production.
With Siemens NX, engineers can navigate complex projects with confidence, backed by a powerful interdisciplinary approach.
Emerging Software Solutions in Mechanical Design
In the dynamic world of mechanical engineering, emerging software solutions have begun carving out a significant niche, transforming how engineers approach design challenges. This section delves into the latest advancements in design software, focusing on innovative platforms that offer unique capabilities. With technology constantly advancing, these solutions provide new avenues for engineers to enhance their workflows, bring creative ideas to life, and ultimately improve project outcomes. The increasing shift towards cloud-based systems, alongside open-source alternatives, cannot be ignored in a landscape where collaboration and accessibility are key.
From embracing cloud-driven design to leveraging open-source frameworks, these tools embody a commitment to enhancing efficiency, accessibility, and flexibility. By incorporating these solutions into their toolkit, mechanical engineers can not only streamline their processes but also foster a collaborative environment that invites diverse perspectives. As these software emerge, understanding their unique offerings helps in optimizing their applicability in real-world projects.
Fusion 360: Cloud-Driven Design
Fusion 360 stands out as a pioneer in cloud-driven design, allowing engineers to work from virtually anywhere. Its user-friendly interface combined with robust functionalities makes it an attractive choice for many professionals. By harnessing the power of the cloud, Fusion 360 offers seamless updates and collaborative features that empower teams to work together in real time.
Some notable Aspekte of Fusion 360 include:
- Integrated CAD, CAM, and CAE Tools: This combination allows for streamlined design processes, ensuring that engineers can iterate and manufacture within the same platform.
- Cloud Storage: Engineers can access their projects anytime, ensuring no work is ever truly โlostโ and giving teams the flexibility to work remotely without barriers.
- Simulation Capabilities: From stress tests to thermal analysis, Fusion 360 helps assess designs through simulations, reducing the likelihood of errors before production.
The flexibility it brings is immense, particularly for smaller teams and startups that might not be able to invest heavily in a suite of separate tools.
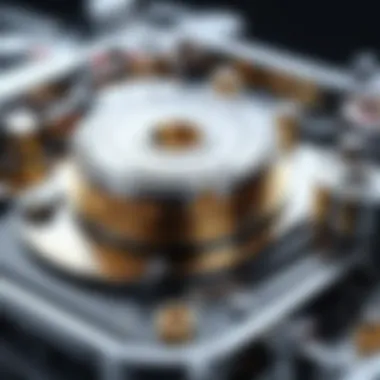
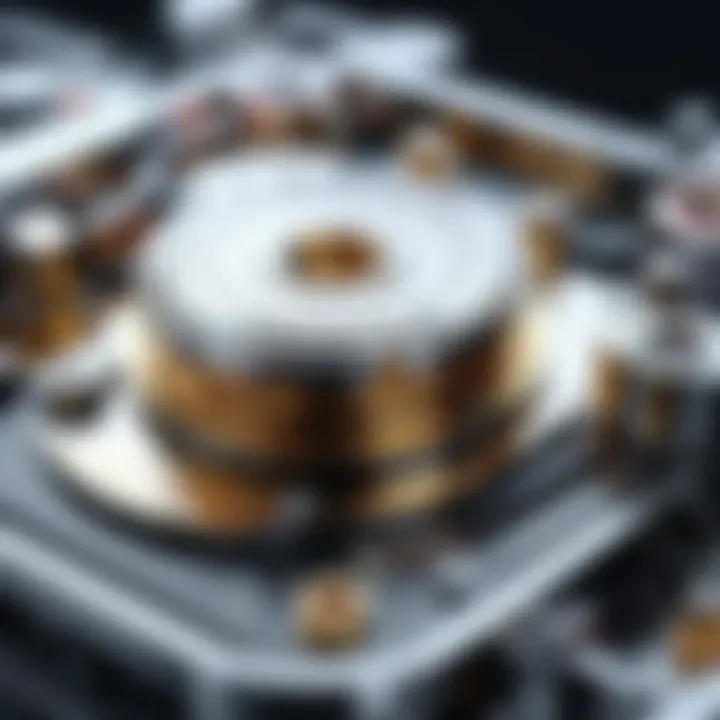
Onshape: Collaborative CAD in the Cloud
Onshape takes collaborative design to the next level with its cloud-based architecture, making it possible for multiple users to work on a project simultaneously. This kind of real-time collaboration is invaluable, especially for teams spread across locations. Onshape's architecture eliminates some challenges of traditional CAD tools which often required extensive file management.
Key features of Onshape include:
- Version Control: Every edit automatically saves, maintaining a full history of changes, which is critical in maintaining clarity and accountability in team projects.
- Robust API: Enables users to customize and build their own apps, extending Onshape's capabilities even further to suit specific needs.
- Mobile Accessibility: Convenient access via mobile devices allows engineers to review and edit designs on the fly, enhancing productivity on-site or during any unexpected downtime.
Onshapeโs cloud-native environment is not just about collaboration; it represents a shift in how engineering teams can approach project management and workflow efficiency.
FreeCAD: Open-Source Alternatives
FreeCAD stands as a beacon of the open-source movement in mechanical design software, making advanced CAD functionalities available to anyone. Unlike proprietary software, FreeCAD offers a non-restrictive environment tailored to design professionals who value flexibility in their tools and processes.
Some of the distinct advantages of FreeCAD are:
- Community-Driven Development: As an open-source platform, users contribute to and improve the software continually. Users can request features, fix bugs, or even develop extensions themselves.
- Modular Architecture: FreeCADโs structure allows users to customize their workspaces significantly, helping diverse users tailor the software to their specific needs.
- Free of Licensing Costs: This removes financial barriers, opening opportunities for small businesses, students, and hobbyists to engage in mechanical design without hefty investment.
The flexibility provided by FreeCAD not only democratizes access to design software, but it also encourages an inventive mindset among users who can experiment without financial constraints.
Emerging software solutions are redefining what's possible for mechanical engineers. By embracing tools such as Fusion 360, Onshape, and FreeCAD, they can elevate their designs and workflows amidst an evolving digital landscape. The tools mentioned here show how technology can facilitate a more collaborative, efficient, and innovative approach to mechanical design.
Comparative Analysis of Leading Software
In a world buzzing with innovation, mechanical engineers find themselves amidst an array of design software options. The importance of comparative analysis cannot be overstated. With numerous alternatives available, each boasting various features, pricing structures, and user experiences, it becomes crucial to dissect these elements. This analysis equips engineers with the insight they require to align their software choices with their professional goals and project requirements. By understanding the nuances of each software, one can avoid the pitfall of choosing a tool based solely on popularity, ensuring it truly meets the specific needs of a project.
Cost-Effectiveness and Licensing Models
When examining cost, itโs necessary to look beyond the sticker price of the software. Different licensing models can significantly impact the total cost of ownership. Some software adopts a subscription model that charges annual fees, making it easy to budget for ongoing expenses. Alternatives like PTC Creo offer perpetual licenses, which can be more economical in the long run for companies committed to one platform.
- Subscription-Based:
- Perpetual Licenses:
- Flexibility in payment.
- Easier to update to the latest version.
- May include cloud storage and support.
- Typically higher upfront costs.
- Ultimate ownership of the software.
- Can be cost-effective over time if used for several years.
Ultimately, whether a software is seen as cost-effective often depends on its intended use. An individual engineer might benefit more from a subscription plan, while larger firms might find it advantageous to buy licenses outright.
User Friendliness and Learning Curve
The ease of use of a design software can mean the difference between getting a project done on time or asking for an extension. The learning curve often varies significantly across platforms. AutoCAD Mechanical, for example, is renowned for its user-friendly interface, which many newcomers find intuitive. However, some industry-specific features can lead to complexities that require time to master.
Factors to consider include:
- Interface Layout: A clear, logical organization often results in faster navigation.
- Documentation and Support: Comprehensive guides and active forums can alleviate the burdens of learning new software.
- Tutorial Availability: A rich array of tutorials can significantly accelerate the learning process.
Itโs important to strike a balance between functionality and usability. Sometimes, more robust software, like Siemens NX, while powerful, can be daunting without proper training.
Integration with Other Tools
In the age of digital workflows, the capacity for design software to integrate seamlessly with other tools is paramount. Designers rarely work in isolation; the ability to transfer files and collaborate with other platforms can enhance productivity and streamline processes.
For instance, choosing a software that easily connects with project management systems or simulation tools can save time and reduce errors. Consider the following integrations:
- Data Import/Export Capabilities: Such provisions are essential for collaborating with others or using various tools across a single project.
- APIs and Extensibility: Software that allows for custom integrations with other applications gives teams flexibility in tailoring their workflow.
For example, Fusion 360 excels in connecting with cloud storage, while software like FreeCAD stands out as an open-source solution that can be customized to integrate with numerous other platforms.
"In competitive industries, harnessing the right software tools means not just surviving, but thriving."
As technological advancements forge ahead, understanding how these software solutions compare can spark significant improvements in workflow efficiency and project outcomes. The nuanced, comparative analysis of leading software should therefore be an integral part of decision-making processes for mechanical engineers.
Impact of Software on Mechanical Engineering Processes
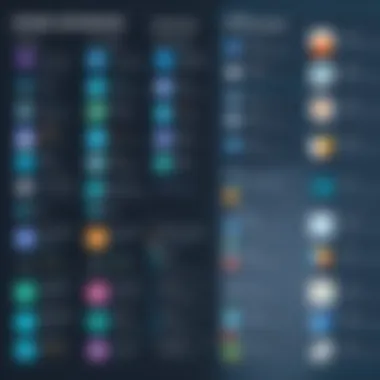
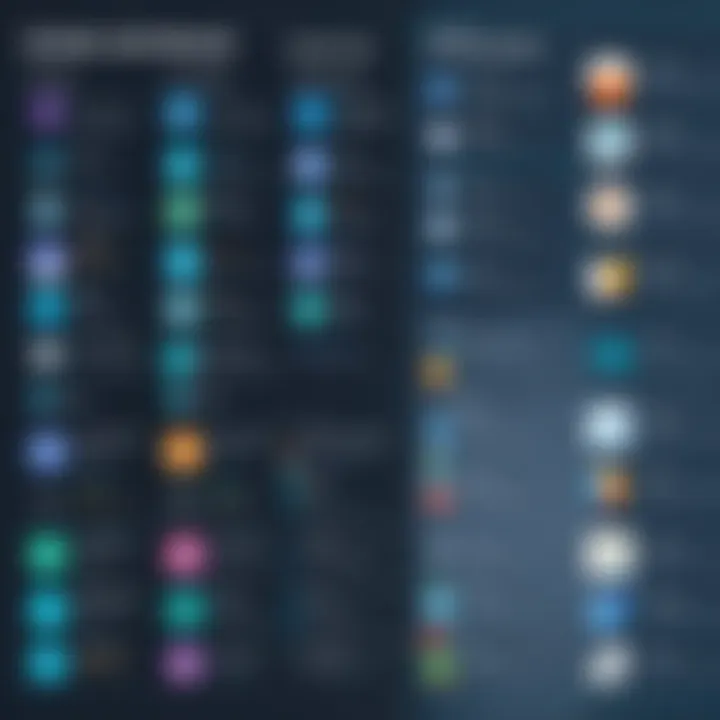
In the field of mechanical engineering, the influence of software cannot be overstated. Mechanical engineers rely on sophisticated tools to translate ideas into practical designs, optimize performance, and manage complexities in projects. With ongoing advancements in technology, the role of software is evolving, particularly in enhancing design productivity and fostering innovation.
The selection of the right software plays a crucial role. It can significantly improve the workflow, lead to cost reductions, and limit the time taken to bring a product from concept to reality. In this landscape, understanding how software impacts various stages of engineering processes is essential for making informed choices that align with project goals.
Enhancing Design Efficiency
Design efficiency directly correlates with productivity in mechanical engineering. Effective design software provides functionalities like parameterized modeling and advanced visualization that streamline the workflows. For example, tools such as Siemens NX can manage complex assemblies while offering real-time feedback on design changes. This capability allows engineers to work smarter and minimize manual rework, which can be both time-consuming and costly.
Key aspects of enhancing design efficiency include:
- Automation Capabilities: Tasks that usually consume manual effort, like documentation or routine simulations, can be automated. This not only saves time but also reduces human error.
- Integrated Tools: Many software options feature built-in tools for analysis, testing, and simulation. By integrating these functions, engineers can instantly see how a design performs under various conditions, enabling quick adjustments.
- User-Friendly Interfaces: A software's usability matters. If engineers can easily navigate the tool and access functionalities without extensive training, they can focus their energies on developing creative solutions rather than fumbling with complex menus.
Overall, enhanced design efficiency translates into faster project turnarounds and can give firms a competitive edge in a crowded marketplace.
Facilitating Innovation and Iteration
The engineering process is iterative by nature. Ideas often start as rough sketches and evolve through multiple iterations before reaching finality. Design software leaps forward by facilitating this cycle of innovation.
With capabilities for rapid prototyping, virtual testing, and collaborative feedback systems, software tools promote a culture where ideas can flourish. Take, for example, Autodesk Fusion 360. It enables real-time collaboration among team members, allowing multiple designers to work on the same project simultaneously, irrespective of their location.
Benefits of using software to facilitate innovation include:
- Virtual Prototyping: Engineers can create prototypes in a virtual environment, experimenting with various designs without physical constraints. This leads to discovering solutions that may not have been apparent in earlier iterations.
- Data-Driven Insights: Software tools leverage data analytics to provide insights on design performance. This feedback can spur innovative ideas and guide engineers toward more efficient solutions.
- Flexibility in Design Changes: Modern design software allows for easy modifications. This flexibility fosters a mindset of experimentation and encourages engineers to think outside the box while pursuing improvements.
In summary, the impact of design software on mechanical engineering processes extends from enhancing efficiency to facilitating a culture of innovation. Recognizing and utilizing the right software is key to a rewarding career in the field, where development cycles can dictate success in the competitive worldwide market.
Future Trends in Mechanical Design Software
As the world of mechanical engineering advances, design software also evolves to meet the growing demands of the industry. Understanding future trends in this field is essential for engineers looking to stay ahead of the curve. With the rise of new technologies, such as artificial intelligence and virtual reality, the landscape of design solutions is set to undergo substantial transformation. Embracing these trends can lead to improved design efficiency, greater innovation, and a more collaborative work environment.
Artificial Intelligence Integration
Artificial intelligence is no longer just a buzzword; it's becoming an integral part of mechanical design software. The ability to analyze vast amounts of data quickly allows AI to provide insights that were previously unattainable. For example, software that incorporates AI can help identify potential design flaws before a project moves into physical prototyping. This type of predictive analysis saves both time and resources, significantly reducing costs.
Another advantage is the automation of repetitive tasks, like generating standard components or simulating conditions. This functionality gives engineers the freedom to focus on creative problem-solving rather than being bogged down by menial tasks. Furthermore, the machine learning capabilities of AI allow software to learn from past projects, suggesting designs or configurations that might not have been considered otherwise.
However, while AI incorporation brings numerous advantages, it also presents challenges. Understanding how to interpret AI-generated suggestions is vital to ensure engineers can make informed decisions, as relying solely on the software's analysis may lead to oversight of critical design aspects.
Advancements in Virtual Reality for Design
Virtual reality is revolutionizing how mechanical engineers approach design. By providing immersive simulations of products in various environments, engineers can visualize and interact with their designs in ways that traditional CAD software cannot offer. This immersive experience can lead to more intuitive design iterations and faster decision-making processes.
One notable application of VR in mechanical design is in prototyping. Instead of building multiple physical prototypes, engineers can create a virtual model that behaves similarly in real-world conditions. This not only streamlines the testing phase but also allows for more flexible adjustments based on user feedback or environmental factors.
Moreover, VR facilitates better collaboration among team members. Teams can connect in a shared virtual space regardless of their physical locations, reviewing designs and suggesting modifications in real-time. This enhances communication and fosters more creative brainstorming sessions.
However, adopting VR technology is not without its hurdles. The initial investment can be significant, and it requires a readiness to adapt to new methods and workflows. Additionally, ensuring equipment compatibility and ongoing technical support will be key considerations for organizations looking to incorporate VR into their design processes.
"The future of mechanical design software will not only shape how we create but also how we think about creating."
In summary, staying attuned to trends like artificial intelligence integration and advancements in virtual reality can position mechanical engineers at the forefront of the industry. By embracing these innovations, they can achieve efficiency gains, foster creativity, and ultimately deliver better designs that meet evolving market needs.
End: Choosing the Right Software
Choosing the right design software is pivotal for mechanical engineers as they navigate the complexities of modern engineering tasks. It not only determines the efficiency of the design process but also impacts overall project outcomes. A thoughtful selection aligns with project needs and organizational goals while facilitating collaboration and innovation.
Evaluating Project Needs
Every mechanical engineering project comes with its own set of requirements. Understanding these specific needs is the first step in selecting appropriate software. Consider the following factors:
- Project Scope: What is the size and complexity of your project? Large teams working on extensive projects may benefit from software that provides comprehensive collaboration tools such as Siemens NX or Fusion 360.
- Industry Standards: Depending on the industryโbe it automotive, aerospace, or manufacturingโthe required software features may differ. For example, CATIA is renowned for its robust capabilities in aerospace designs.
- Budget Constraints: Cost is often a significant factor. Evaluate not just initial costs but also long-term expenses related to updates, licenses, and support. Software like PTC Creo provides flexible licensing that can suit various budget needs while not sacrificing functionality.
By asking these questions, teams can narrow down choices, ultimately leading to a better fit for the project's demands.
The Importance of Ongoing Training and Support
In the fast-paced world of engineering, staying updated with software advancements is crucial. Ongoing training and support ensure that engineers can utilize all the tools available to them. This is particularly important in software as complex as AutoCAD Mechanical or SolidWorks. Here's why prioritizing training matters:
- Maximized Efficiency: Regular training helps engineers make the most of the software's features, leading to streamlined workflows and reduced error rates.
- Adaptation to Updates: Software is regularly updated, introducing new features and capabilities. Continuous training ensures that the team is not left behind and can integrate these updates effectively.
- Problem Resolution: Having access to support means that any issues can be resolved swiftly, minimizing potential downtimes that could delay project timelines.